The Theory of R-value Relativity: The impact of thermal conductivity on building enclosure durability
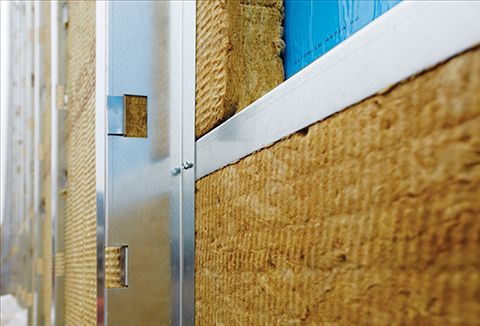
By Rockford Boyer, B. Arch. Sc., BSSO
When designers are deciding which insulation products to specify for a given project, two questions come to mind: ‘What is the R-value?’ and ‘What is the permeance?’ The answer to both these queries is, ‘It is all relative.’ If Einstein had not been so focused on the speed of light, he would have had the time to establish the third theory of relativity—R-value relativity. Thermal insulation’s effective performance and permeance properties are relative and dependent upon project location—specifically, temperature and climate. In other words, a building assembly will perform differently in Victoria, than it would in Whitehorse. Therefore, it is essential to understand the dynamics of building products under regional climatic conditions in order to increase overall building durability.
Generalizations are not effective
Insulation types should not be treated equally, as there is a wide range of varying performance characteristics. However, some codes and standards organizations are pushing for equal testing on these types of products. Buildings are not constructed in laboratories, so why do these arguably semi-irrelevant tests—which have no bearing on real life—persist in-situ scenarios?
If buildings were built with the quality and precision accomplished in the laboratory, many failures would not exist. Obviously, since the industry spends millions of dollars annually on repairs, a better mechanism for relevant building components and assemblies testing needs to be in place.
Designers should ask manufacturers and product suppliers for tested data relevant for their applications and locations. It is understandable codes and standards are necessary for marketing value. However, project teams should consider additional questions and analysis outside the realm of standardized testing.
In lay terms, R-value is defined as a material’s resistance to heat transfer. One might assume the higher the R-value, the lower the thermal conductivity (k-value)––resulting in higher performance. However, the answer is again relative. Three mechanisms of heat transfer cumulatively determine the relativity of the performance:
- conduction;
- convection; and
- radiation.
In general, residential and commercial insulations use an ASTM standard test method to measure heat flow through a given medium. In the case of insulation, the standardized test for determining heat flow is ASTM C518, Standard Test Method for Steady-state Thermal Transmission Properties by Means of the Heat Flow Meter Apparatus. This standardized approach is an accurate way to measure and determine the R-value of a product. However, the mean temperature to report R-value is stated at 24 C (75 F). It does not make sense to insulate buildings from room temperature, but using this mean temperature of 24 C results in higher repeatable accuracy. So, is it the intention of this test procedure to produce a more accurate result to the nearest third decimal place or to actually provide valuable and applicable information for designers to increase energy efficiency and envelope durability? As an industry, a great deal of knowledge and awareness are required to fully understand how temperature-dependent thermal conductivity (TDTC) impacts building and component durability. As a designer, one of the most important questions is to ask, ‘What the R-value is of a product for the project’s particular climate zone?’
Researchers, organizations, and educational institutions conduct research to understand how temperature affects insulation material’s thermal conductivity. Organizations such as the National Roofing Contractors Association (NRCA), Building Science Consulting Inc. (BSCI), RDH, and the University of Waterloo (Ontario), all invest time, money, and resources to promote the in-situ performance of insulation under realistic conditions. Research conducted by these various organizations determined R-values are, in fact, based on the temperatures with which they interact.
Depending on the insulation type (whether mineral fibre or foam plastic), three or four major variables could affect the material’s R-value performance. Conduction and convection exhibit a linear relationship between temperature and R-value, whereas radiation impacts R-value to the fourth power. Additionally, blowing agents used in certain foam plastic insulations are typically not taken into account but can have an adverse affect on R-value. These blowing agents have both a condensation point and a boiling point—meaning they have the potential to change from one phase to another based on ambient temperatures. If the temperature is low enough, condensation occurs in the blowing agent; this increased thermal conductivity of the liquid in the cell significantly reduces the R-value. Figure 1 illustrates heat transfer mechanisms and the effects of condensation in the cells. Moisture present within insulation can drastically reduce insulation’s efficiency.
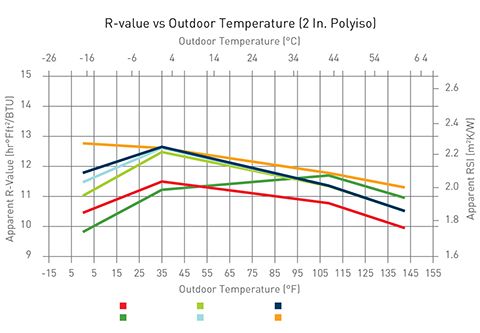