Staying current with Canada’s energy code
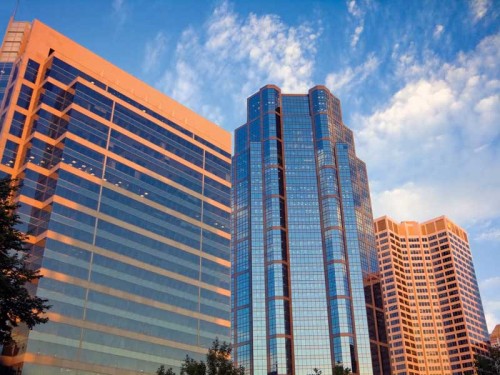
By John Burrows, P.Eng., and Jim Gallagher
The efficiency of new buildings designed to meet the 2011 National Energy Code of Canada for Buildings (NECB) will be significantly better than that of most older structures. It replaces the 1997 Model National Energy Code for Buildings (MNECB), and will become a requirement in the adopting provinces and territories. Consequently, it is critical architects, specifiers, engineers, owners, and other members of a project team understand its requirements. (This article is based on material published by the National Research Council of Canada (NRC). For more detailed information about NECB, design/construction professionals can refer to the free, online presentations available at NRC’s National Codes website. Visit www.nationalcodes.nrc.gc.ca/eng/presentations/2011_necb_presentations.shtml. To order a copy of the 2011 code, visit www.nrc.gc.ca/virtualstore).
The code applies to new buildings and additions, yielding an average of 26 per cent overall energy performance improvement compared to MNECB. It provides designers more flexibility by offering several compliance paths. It addresses the energy used by the building, irrespective of the energy source, with no exemption for any type of assembly construction or occupancy.
However, its scope does not include housing and small buildings covered by Part 9 of the National Building Code of Canada (NBC). Instead, a new section of NBC Part 9 will introduce updated energy requirements for these buildings. NECB also does not apply to farm buildings.
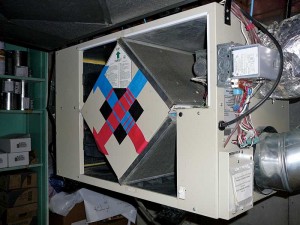
Photos courtesy NRC Construction
The code’s development was initiated by the Canadian Commission on Building and Fire Codes (CCBFC) in response to stakeholder requests to add a new objective on energy efficiency to the National Model Construction Codes. It is the result of an extensive consultation process involving representatives from Canadian industry, multiple levels of government (i.e. federal, provincial, territorial, and municipal), the construction industry, and the general public. Both the National Research Council-Institute (through its construction research arm, NRC Construction) and Natural Resources Canada (NRCan) provided technical support. The latter supplied funding as part of its commitment to improve the built environment’s energy efficiency and reduce greenhouse gas (GHG) emissions.
This article provides detailed information on the energy requirements for NECB, Part 3 (“Building Envelope”), and also outlines:
- Part 4 (“Lighting”);
- Part 5 (“Heating, Ventilating, and Air-conditioning Systems”);
- Part 6 (“Service Water Heating”);
- Part 7 (“Electrical Power Systems and Motors”); and
- Part 8 (“Building Energy Performance Compliance Path”).
The code offers three compliance paths:
- prescriptive path, which stipulates what needs to be done to comply;
- trade-off path, which provides more flexibility but cannot be used for Part 7 or between provisions in different parts; and
- performance path (i.e. Part 8), which is a whole-building modelling approach.
Part 3, building envelope
Part 3 of NECB deals with the building envelope, with various thermal/moisture protection components discussed in the paragraphs
that follow.
Prescriptive path: insulation
There are provisions for protecting insulation against degradation of thermal properties due to:
- air leakage or convection;
- wetting; or
- moisture bypassing the plane of thermal resistance.
There are also requirements for the continuity of insulation so prescribed levels are provided over the entire building envelope. Maximum overall thermal transmittances (i.e. U-values) are given for above-ground opaque building assemblies, fenestration, doors and access hatches, and assemblies in contact with the ground. The code’s insulation level demands are based on the heating degree-days for given locations, as found in NBC’s Appendix C.
The climatic zones in NECB have been set using 1000 heating degree-day gradations. The zone names are the same as those used in American Society of Heating, Refrigerating, and Air-conditioning Engineers (ASHRAE) 90.1, Energy Standard for Buildings Except Low-rise Residential Buildings, except Zone 7 is split into two 1000 degree-day zones called 7A and 7B to better reflect the reality of the Canadian climate.
Prescriptive path: above-ground assemblies
The prescriptive requirements set a maximum overall U-value for the building enclosure’s above-ground walls, roofs, and floors that vary according to the heating degree-day location of the building.
Zone 4 is for areas with less than 3000 heating degree-days—examples include Victoria and the B.C. Lower Mainland. For these locales, the maximum overall U-value for walls is 0.315, which is equivalent to a minimum effective RSI of 3.17 or approximately R-18.
Zone 8 includes areas with 7000 heating degree-days or more, such as most of the Yukon, Northwest Territories, and Nunavut. Here, the maximum overall U-value for walls is 0.183, which translates to a minimum effective RSI of 5.46 or R-31. Roofs and floors in Zone 8 have a maximum overall U-value of 0.142—a minimum effective RSI of 7.04 or R-40.
All the maximum allowable U-values are reduced by 20 per cent (i.e. more stringent) for various assemblies containing embedded radiant heating and/or cooling cables, pipes, or membranes.