Ensuring Durable Concrete: Marine infrastructure
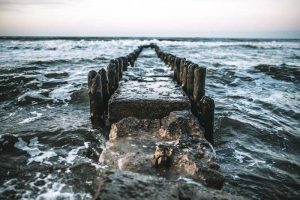
By Jackson So, B.A.Sc., EIT
Major infrastructure that affects the lives of tens of thousands on a daily basis must last for its expected life (at the very least)—otherwise, a ripple effect is caused to government budgets, negatively affecting each citizen in some capacity. When infrastructure fails prematurely, action must be taken to discover why it happened, enabling the engineering community and infrastructure owners/managers to amend the practices going forward to preserve durable growth throughout city networks.
Failing structures may fall into a spectrum of different issues, but the underlying cause of prematurely problematic concrete is often the same—water penetration. Rainwater and humidity can find their way into the porous networks within the concrete through the smallest entry point; the result is slow, but often catastrophic, damage to the structure. Given enough time, water will support deterioration, corrosion, rusting, and/or change to all building materials.
In particular, any concrete structure in close proximity with water faces myriad life-shortening processes. Reinforced concrete infrastructure, found in marine environments, commonly face reduced life spans due to exposure to extreme environmental conditions, which allow water and waterborne chlorides to penetrate through the concrete to the reinforcing steel. This contact results in corrosion and expansive cracking, leading to premature deterioration.
Bridges, tunnels, and retaining walls are all types of infrastructure that are affected by the highly destructive nature of marine environments. Other types of infrastructure may be less obvious, such as sewer pipes or water tanks, but often must deal with high hydrostatic pressure and the corrosive elements that are brought in by seawater nonetheless.
How water attacks concrete structures
Since nature cannot be ‘stopped,’ design/construction professionals must instead direct careful attention to how nature operates and plan accordingly when designing, constructing, and maintaining concrete structures. Not all damage is the result of spectacular floods, storms, or newsworthy global-warming events—some are slow and unseen, but the outcome can be just as damaging.
All concrete infrastructure found in or near marine environments will face reduced life spans unless steps are taken to protect them. They are at a higher risk of corrosion due to the constant wet-dry-wet cycle that forces water through capillary tracts and micro-pores found in the concrete. When adding in the extreme freeze/thaw weather conditions experienced throughout Canada, the protection of these structures must be of utmost importance.
Water permeability ultimately determines the rate of deterioration, with some of the deterioration mechanisms threatening marine concrete infrastructure being:
- steel reinforcement corrosion;
- chloride attack;
- sulfate attack;
- alkali aggregate reaction (AAR); and
- freeze/thaw cycles.
Corrosion of steel reinforcement
There are three essential components necessary for corrosion to take place in reinforced concrete:
- electrolyte for ion transfer (e.g. water);
- conductor for electron transfer (e.g. steel
reinforcement); and - oxygen.
Eliminating one of these components will mitigate the damages due to corrosion. This is both why there is no corrosion in dry concrete, and why it is important to have low-permeability concrete to prevent the movement of water and the harmful chemicals in solution from reaching the steel reinforcements.
Overall, concrete serves as a great host for the rebar. Due to the former material’s high alkalinity, the latter develops a passive layer that provides a protective barrier to the steel. In this state, concrete normally provides excellent corrosion protection, but the passive layer can be broken down over time due to atmospheric carbon dioxide. This causes carbonation, which lowers the pH of the concrete and destabilizes the passive layer. However, this is a slow process and the overall rate depends on the density of concrete and humidity of the exposed environment. Durable concrete with low permeability can reduce the rate of carbonation, in addition to slowing the rate of water penetration necessary for corrosion to occur.