Designing With Stainless Steel: Bioclimatic hybrid façades
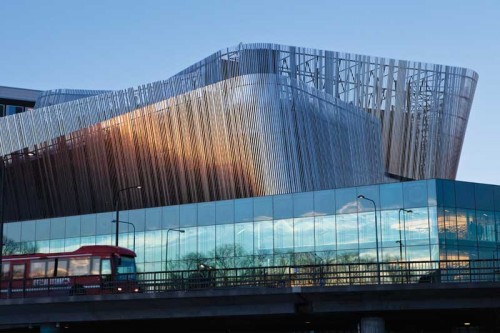
By Catherine Houska, CSI
An international design revolution is incorporating both traditional and new concepts to create bioclimatic sustainable architecture. Building energy reduction is a key goal for new and renovation projects designed to these principles, but it must be balanced against occupant well-being and the desire for fresh air and natural light.
Exterior walls are being transformed from relatively simple climate defensive mechanisms to more active membranes. Innovative hybrid second-skin designs incorporating shading systems are being used on award-winning projects around the world, and these concepts could be applied to a much broader range of buildings. (This author would like to acknowledge the International Molybdenum Association (IMOA) and the Nickel Institute for its assistance in the preparation of this article).
Lifecycle assessments (LCAs) that consider materials’ longevity are important because these exterior elements must withstand potentially corrosive environments with minimal or no maintenance. This can make stainless steel a logical choice for a multitude of demanding exterior applications.
Bioclimatic architecture refers to designing buildings and spaces (interior and exterior) using local climatic conditions to improve thermal and visual comfort. These designs incorporate systems that provide protection from summer sun, reduce winter heat loss, and make use of the environment (e.g. sun, air, wind, vegetation, water, soil, and sky) for heating, cooling, and lighting buildings.
If energy reduction was the only consideration, the optimal structure would have heavily insulated walls with no windows and recycled air. However, a balance must be struck with human health and productivity. Bioclimatic design elements go beyond adequate insulation and adjust environmental conditions so building inhabitants find them comfortable and pleasant. Designing with the local climate is both economical and ecologically sound.
Hybrid second-skin façades
Hybrid second-skin designs can increase the building inhabitants’ connection with their surroundings. Exterior surfaces are shaded from the sun, reducing cooling requirements while still allowing daylight to enter. Some also shelter exterior surfaces from wind during the winter, reducing heating requirements. Both active mechanical systems that constantly adjust to the environment and fixed passive systems are used. All the systems can assist with managing outer and inner climates through varying degrees of integration with the building systems and improved natural ventilation and lighting.
These façades can be installed on existing and new structures. Various sun-screening technologies include:
- louvres;
- woven mesh;
- perforated screens; and
- green (i.e. vegetated plant) façade screens.
In new construction, these systems can transform the appearance of lower-cost buildings—such as simple concrete and glass shapes—at a much more reasonable price than a more elaborate curtain wall. On existing buildings, they can reduce energy expenses while updating the appearance.
Active second-skin façades
There are many variations on active second-skin façades. Hybrid systems employ an operable shading system over the insulated glass façade, which maybe between inner and outer glass layers or be the outermost wall. The two layers can be from 0.2 to 2 m (0.7 to 6.6 ft) apart, and incorporate integrated sunshades and natural ventilation. All have computer-controlled mechanical operating systems that work in co-operation with the building’s heating and cooling systems, making it possible for them to respond dynamically to varying conditions. By adjusting to the trajectory of the sun’s rays, they maximize the benefits of solar radiation while minimizing heat gain.
Energy is necessary to operate these assemblies, and maintenance of the mechanical and sensing systems is required. Active second-skin façades have been particularly popular in Europe, Asia, and Australia, although some of the earliest examples are in North America (i.e. Occidental Chemical Centre, Niagara Falls, N.Y., completed in 1980).
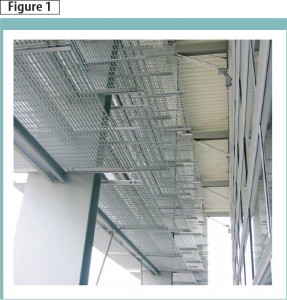
Photo courtesy Centro Inox
Passive second-skin façades
The simplest second-skin façades have fixed semi-permeable membranes that allow the building to breathe and can consist of woven mesh, perforated sheets, green plant screens, or other forms of shading. These are popular for low-maintenance applications such as public buildings (Figure 1). Additionally, ‘living walls’ or ‘vertical gardens’ of plants––like those installed at Vancouver International Airport (i.e. Aquaquest at the Marilyn Blusson Learning Centre) and at the Vancouver Aquarium––provide some of the same sustainable advantages as green roofs and often use specially designed, corrosion-resistant, angled stainless steel planters to hold soil or growth media. All these systems are interfaces between the building’s internal and external climates, but are not mechanically tied to the building’s internal climate management systems.
Like active screens, passive second-skin façades provide at least some shelter from harsh weather by reducing the impact of rain and direct sunshine. Ideal for projects where minimum maintenance is expected or where lower technology solutions are preferred, they are growing in popularity around the world.
Stainless steel selection
The term ‘stainless steel’ refers to a family of alloys that provide varying levels of corrosion resistance, strength, and formability. The most commonly specified stainless steels are Types 304/304L, 316/316L, and to a lesser extent, 2205, but many other grades have been used. Stainless steels provide much higher corrosion resistance than other common architectural metals, particularly when there is pollution and chloride salt exposure (primarily de-icing and coastal salt). There are numerous articles and industry association brochures to assist with stainless steel selection. (For further information on stainless steel selection and design, see various articles by this author. They include “Sustainable Stainless Steel Architectural Design,” Construction Canada (September 2009), “Designing on the Waterfront,” The Construction Specifier (November 2007), “Pushing the Design Envelope with Structural Stainless Steel,” by this author and Kirk Wilson, The Construction Specifier (April 2007), “Architectural Metal Corrosion: The de-icing salt threat” The Construction Specifier (December 2006), “Metals for Corrosion Resistance: Part II” The Construction Specifier (November 2000). More information can also be found in Guidelines for Corrosion Prevention by the Nickel Institute (pub. 11 024), and in Which Stainless Steel Should be Specified for Exterior Applications by the International Molybdenum Association [IMOA]).
Type 304/304L is generally appropriate for climate-controlled indoor and mild outdoor applications with low levels of urban pollution. If there will be some chloride salt exposure or higher pollution levels, Type 304 should be specified with a smooth finish and regular cleaning. The possibility of some staining between cleanings should be expected.
Since Type 316/316L contains a molybdenum addition, it is more corrosion-resistant than Type 304. It is usually suggested for exposure to low to moderately corrosive coastal and de-icing chloride salts, and moderate industrial or higher urban pollution levels. It was used for many of the projects that will be discussed in this article because of these conditions. It does not provide sufficient corrosion resistance for applications with high surface chloride salt accumulations or exposure to salt-water spray or splashing unless a smooth finish is specified and there will be regular cleaning. Care should be taken in specifying tightly-woven and cable products since chloride crevice corrosion can occur if there is exposure to high enough salt levels and a more corrosion-resistant stainless steel may be required.
Duplex stainless steels like 2205 are significantly stronger than non-cold-worked Types 304 and 316 and common structural carbon steels. Some, like 2205, can provide a significant improvement in corrosion resistance. Their high strength and corrosion resistance has made them an increasingly attractive choice for some applications. More resistant stainless steels than 2205 can be obtained. When an environment appears severe, the advice of a corrosion specialist should be obtained.
Since exterior air and humidity circulate through sunscreens, and segments are often sheltered from rain-washing, these spaces can be more corrosive than those boldly exposed to rain-washing. Designers should consider whether rain or manual washing is likely during material selection.
Sustainable design benefits
On average, international stainless steel production contains about 60 per cent recycled scrap content, and over 92 per cent of the stainless steel used in architecture, building, and construction is recycled at the end of service into new stainless steel. (For more information, visit the International Stainless Steel Forum (ISSF) website at www.worldstainless.org). In countries with a high historical use of stainless steel, the recycled content may be as much as 90 per cent for Types 304/304L and 316/316L.
Numerous studies around the world have examined runoff from various materials (e.g. asphalt, metal, clay tile, and concrete). The primary purpose has been to determine whether the runoff is potentially toxic to humans, plants, or wildlife. Stainless steel has extremely low runoff levels (often below detectable limits), and it is not a biocide or otherwise toxic to the environment.
German corporate campus
A seven-building corporate campus in Essen, Germany, designed by JSWD Architekten and Chaix & Morel, was awarded a pre-certificate in Gold from the German Sustainable Building Council (DGNB). (Additional information can be found in the October 2010 issue of ThyssenKrupp Quarter and company press releases). Based on the new German Certification for Sustainable Buildings, its energy consumption is expected to be 20 to 30 per cent below statutory requirements.
All the buildings are simple glazed shapes made interesting by their external Type 316 stainless steel sunshade systems. Building Q2––the corporate conference and training centre––has custom perforated stainless steel sunscreens that are a passive second skin. Active motorized sunshade second skin-façades were used on Building Q1, which has horizontal slats.
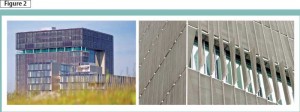
Photos courtesy ThyssenKrupp AG
Buildings Q5 and Q7 have a playful combination of horizontal and vertical stainless steel slats. The solar control systems on both buildings have moveable triangular, square, and trapezoidal fins that both save energy and create a unique appearance. Used in combination with natural ventilation and geothermal heating and cooling, the systems eliminated the need for air-conditioning and greatly reduced winter heating requirements (Figure 2).
The Type 316 stainless steel slats were mounted on vertical shafts, which rotate to adjust their position. A dull abrasive-blasted finish was applied to one side of each slat and a highly polished finish to the other. Both seasonal sun position and current weather data are used by the computer system to adjust slat position to maximize natural lighting while minimizing summer heat gain.
The reflective surface faces inward and helps bring more natural light into the building while shielding it from sun and weather. Since this inner surface will not be naturally cleaned by rain, it would have been more prone to dirt accumulation and corrosion if a smoother finish had not been specified. The system can be used during all weather conditions—including high winds—and shields the building exteriors from harsh weather.
Council House 2
Melbourne, Australia’s 10-storey Council House No. 2 (CH2)—a multi-award winning building completed in 2006—was the first commercial building to achieve Green Building Council of Australia’s (GBCA’s) highest possible Green Star ‘6’ rating. The architect, DesignInc, reconsidered every aspect of the building during design. Relative to the city’s Council House No. 1, it uses 85 per cent less electricity, 87 per cent less gas, and 72 per cent less potable water; carbon dioxide (CO2) emissions associated with building operation were also reduced by about 60 per cent. (For more information, see “CH2 6 Stars, but How Does it Work?” and “CH2 6 Stars, but is it Architecture?” in the January/February 2007 issue of Australian Architecture).
Since air-conditioning is typically responsible for half the energy consumption of a typical Melbourne building, the designer used both active and passive sunscreens, natural ventilation, and conductive cooling of the ceilings to reduce energy requirements. The building’s west side has an active second-skin façade of timber slat sunscreens covering the fully glazed exterior. They are supported by a lightweight Type 316 stainless steel tension cable system, allowing them to be pivoted vertically so they open and close in response to the time and sun’s angle.