Concrete Cracking Problems: A modern-day phenomenon?
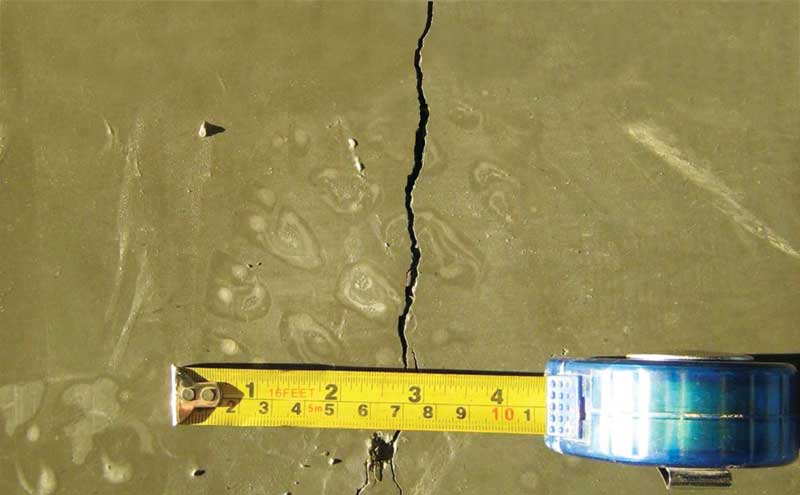
By Paul Jeffs
Anecdotal evidence suggests cracking of concrete structures and components appears to be on the rise, often resulting in conflict between involved parties. Sometimes described as severe and/or excessive, it appears the cracks occurred even when specifications were strictly followed and the concrete designed, supplied, placed, and cured in accordance with formal standards and good practices of the construction industry. Often, cracks occurred soon after the concrete hardened, but then continued to grow over many months or even years.
This author believes the increase in the occurrence of cracks is caused by modern concrete mixtures that lead to a higher magnitude of naturally occurring autogenous shrinkage. The problem is compounded by the fact that stresses developed within the concrete by the resultant volume change affected by autogenous shrinkage are in addition to the known problems associated with drying shrinkage cracking—the latter having been shown to typically follow or combine with the former to aggravate the extent and severity of the cracks.
When cracking problems occur, investigation will typically focus on the practices and factors causing or influencing excessive drying shrinkage, such as excessive workability, rapid drying conditions, and poor curing practices. However, although drying shrinkage certainly should be considered when investigating the potential cause of excessive cracking, the influence of autogenous shrinkage is typically overlooked, but can sometimes be dramatically more important. Many researchers believe autogenous shrinkage strains can be at least equal to strains caused by drying shrinkage and, under certain conditions, can be considerably greater.
What is autogenous shrinkage?
Autogenous shrinkage and its adverse effects on hardened concrete have been well-studied by researchers and concrete scientists for decades, but the phenomenon remains a mystery to many who are involved at the grassroots of the concrete industry, and possibly even to a large number of seasoned practitioners. Perhaps one of the reasons for this may be the natural reluctance of the various involved parties to publicize their problems.
In simple terms, the complex phenomenon can be described as a physical, volume-reducing response to chemical reactions generated by the natural hydration of the cementitious binder, but occurring without moisture transfer to the environment. (Another form of shrinkage known as chemical shrinkage—often confused with autogenous shrinkage—also takes place because of cement hydration reactions, but this occurs very early and has no influence on the potential for cracking after hardening. It will therefore not be discussed further within this article.) Autogenous shrinkage can also be described as being the result of internal self-desiccation—a reduction in the amount of moisture that could otherwise be available for binder hydration reactions.
Self-desiccation
The American Concrete Institute (ACI) defines self-desiccation as:
the removal of free water by chemical reaction so as to leave insufficient water to cover the solid surfaces and to cause a decrease in relative humidity of the system.
However, the International Union of Laboratories and Experts in Construction Materials, Systems, and Structures’ (RILEM) book TC 196-ICC, State-of-the-Art Report on Internal Curing of Concrete, goes somewhat further by defining it as:
the reduction in internal relative humidity of a sealed system when empty pores are generated. This occurs when chemical shrinkage takes place at the stage where the paste matrix has developed a self-supportive skeleton, and the chemical shrinkage is larger than the autogenous shrinkage.
Self-desiccation can lead to a lower hydration compared with a moist-cured paste; this is because cement gel can only form within a water-filled space. In addition, according to the textbook Properties of Concrete, by expert Adam Neville, because hydration of a sealed system can proceed only if the amount of water present in the paste is at least twice that of the water already combined, self-desiccation becomes important for concrete mixtures when the water/cement (w/c) ratio is below about 0.50.
Mechanisms of autogenous shrinkage
As water is lost to internal autogenous hydration reactions, tensile stresses are generated in a similar mechanism that occurs when water is lost by evaporation to cause drying shrinkage. Both of these mechanisms can result in the formation of cracks. The most widely accepted theory to explain the volume change that subsequently occurs is capillary tension. This develops within the cement paste pores as moisture is lost and menisci are thereby formed. However, drying shrinkage focuses the stresses at the exposed concrete surfaces, whereas autogenous shrinkage issues occur throughout the mass of concrete.
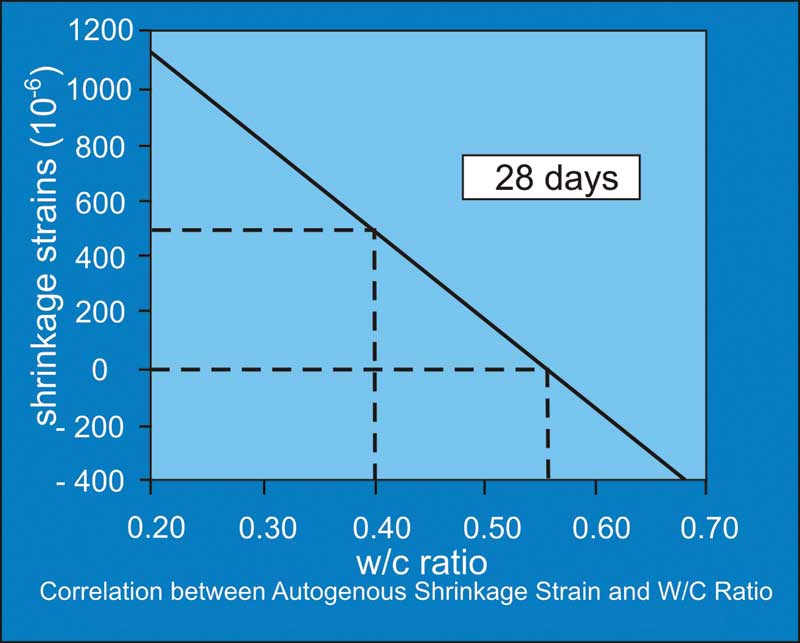
Researchers and experts such as Neville have explained the strains developed by the formation of the menisci pull the cement paste closer together and register as a volume reduction. If strains continue to be generated to the extent the tensile stresses exceed the strength resistance, the concrete will crack. Researchers have also indicated in high-strength concrete with a low w/c ratio, the finer pore structure within the cement paste causes the menisci to have a greater radius of curvature. These menisci create a larger compressive stress on the pore walls, thus generating greater autogenous volume change as the paste is pulled inward.
Laboratory studies have confirmed autogenous shrinkage typically occurs at a very early age, but, under certain conditions, it can continue over several days and even weeks. As the rate of creep and relaxation in new hardened concrete can be high, the stresses that occur at early ages can rapidly disappear. However, depending on the extent and severity of the influencing factors, internal microscopic cracks can form—although, at early ages, they may have little adverse effect on the short-term durability of the concrete. Unfortunately, should autogenous shrinkage continue to develop, the microcracks can subsequently widen and propagate to facilitate the ingress of moisture. After several weeks, even months, the influence of drying and carbonation shrinkage means more cracks may occur and the existing ones could further widen and lengthen. According to ACI 446.1R, Fracture Mechanics of Concrete: Concepts, Models, and Determination of Material Properties, cracks may propagate at much lower stresses than are required to cause crack initiation.
The influence of free-mixing water content on the strains generated by the autogenous shrinkage resulting from self-desiccation has been well-researched, with typical conclusions indicating strains can be significant as the w/c ratio becomes less than 0.40 (Figure 1). However, it has also been claimed variations in cementitious binder chemistry and particle fineness can result in autogenous shrinkage becoming significant when w/c ratio limits vary between 0.36 and 0.48.