Is B.C. the leader in mass timber?
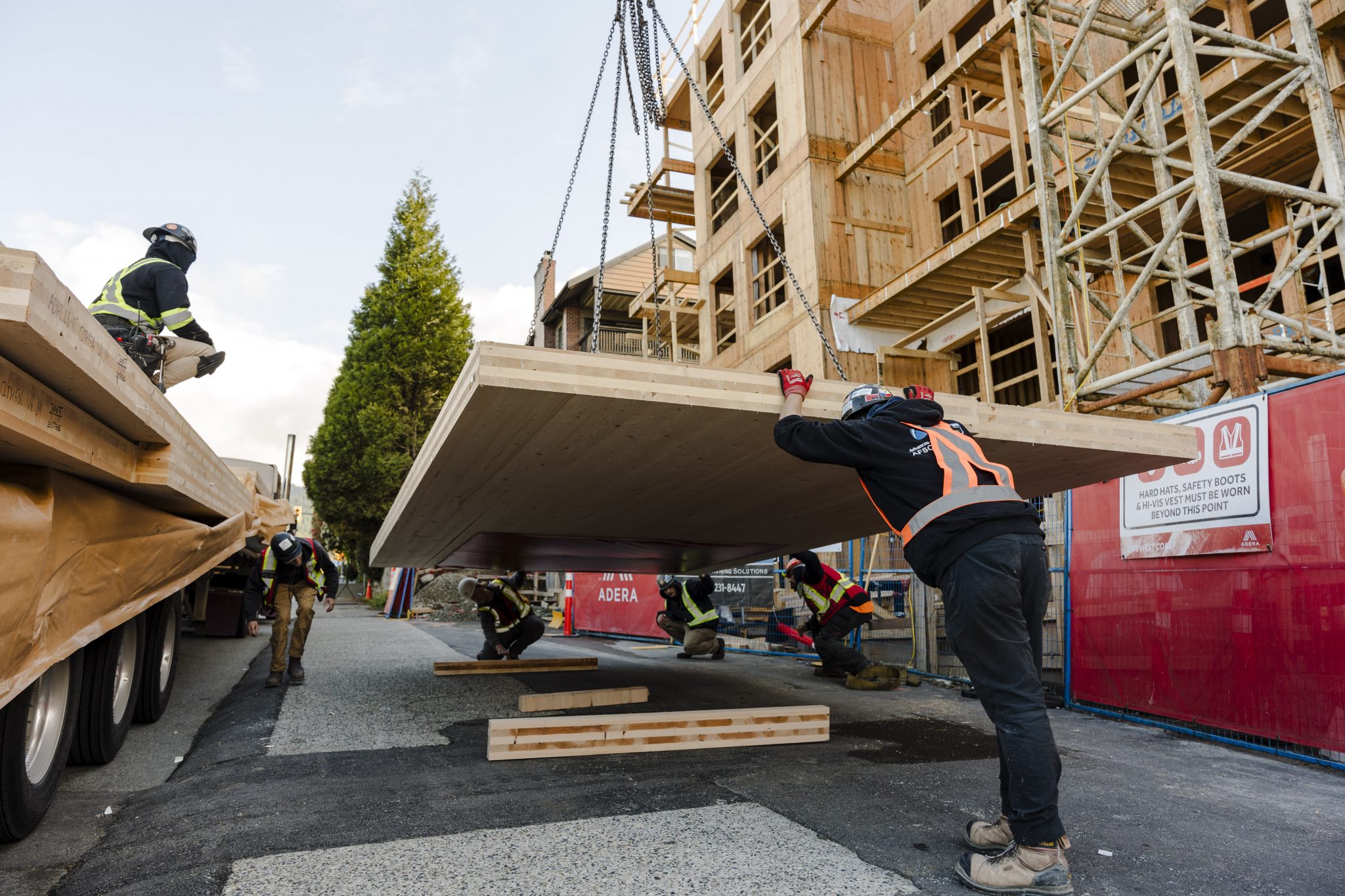
Eric Andreasen, the vice-president of marketing and sales at Adera Development, spoke to Tanya Martins of Construction Canada and shed light on how B.C. is on its way to becoming the leader in mass timber development globally.
Does B.C. still lead in the design and implementation of mass timber systems compared to other jurisdictions? How is that leadership being measured?
British Columbia remains at the forefront of mass timber design and implementation globally. The province has the highest number of mass timber buildings per capita of any other place in North America, and leads the country with more than 285 mass timber buildings.
B.C.’s Mass Timber Action Plan has driven the expansion of mass timber construction, manufacturing, and workforce development across the province. This has increased the number of mass timber buildings and positioned B.C. as a critical exporter of knowledge and products to international markets. Metrics such as overall building count, advancements in carbon reduction, and the adoption of encapsulated mass timber construction (EMTC) standards in other regions all reflect our sustained leadership.
How have B.C.’s amendments to the BC Building Code (BCBC) impacted design flexibility, structural performance, or cost efficiency?
The updates to the BCBC in 2024 have been pivotal for the industry. The recent increase in the allowable height for EMTC to 18 storeys, coupled with the expanded range of building types permitted—including restaurants, shops, schools, care facilities, and warehouses—marks a new era of design flexibility, where developers can build almost any type of building using mass timber. These amendments empower architects and developers to consider mass timber in previously restrictive applications without sacrificing performance and open up the markets for mass timber products. For instance, many buildings often feature a variety of complex elements at ground level, but as you move upward, the structure becomes more straightforward. In a six-storey building, these elements at ground level concentrate on the overall impact on the building. This ability to build taller with mass timber not only streamlines the design but also makes construction more cost-effective compared to the intricacies found at the base.
Additionally, the amendments could bolster B.C.’s economy by promoting the use of locally sourced forest products and employing local workers to construct much-needed affordable housing.
Structurally, the amendments reinforce the confidence in the seismic and fire-resistant capacities of mass timber. Mass timber does not burn like conventional wood due to its density and the limited surface area available for fuel-to-air interaction. The expanded encapsulation rules allow greater exposure of timber in certain applications, blending esthetics with practicality while meeting safety standards.
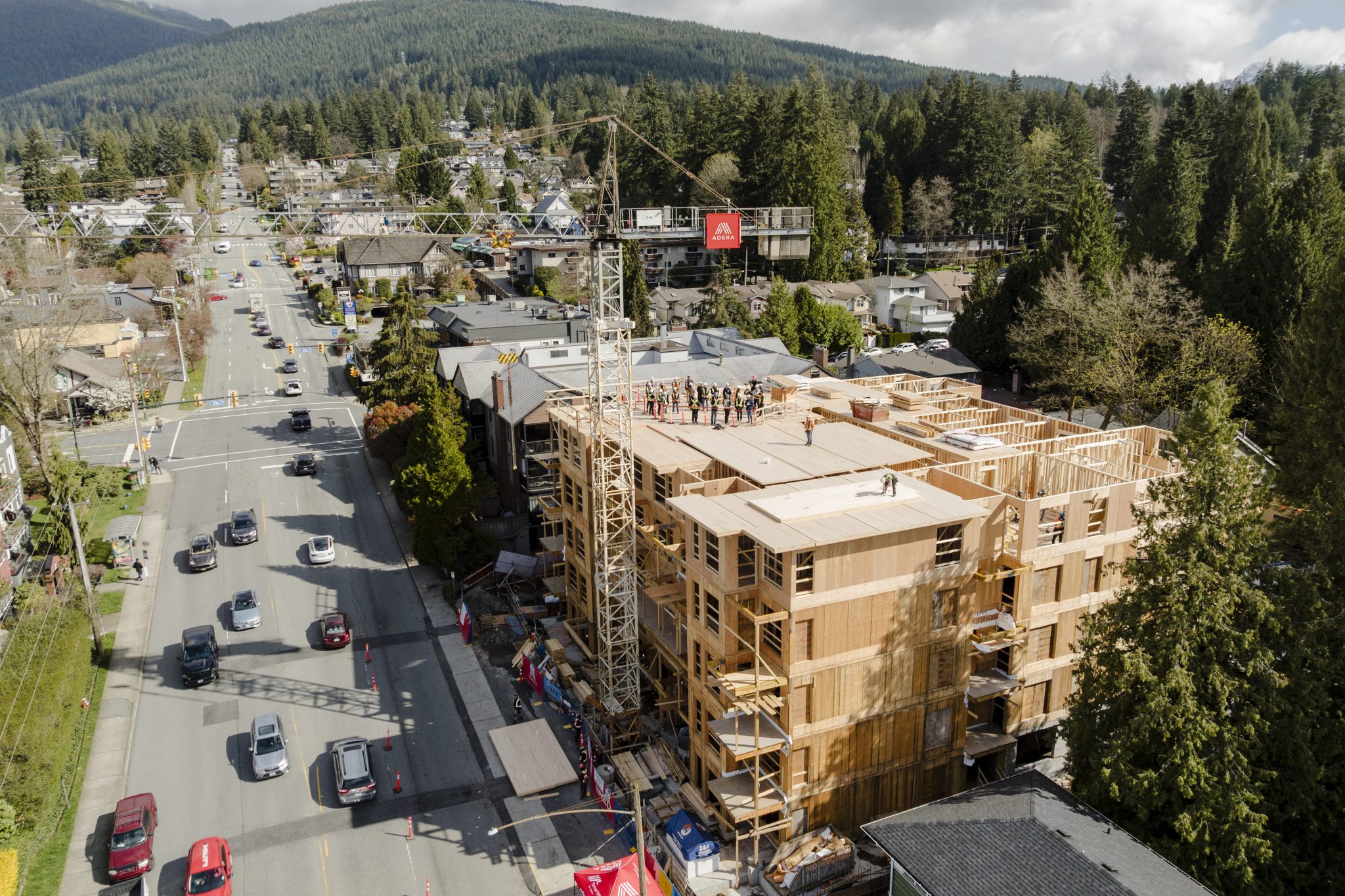
What are the current technical barriers that might limit the broader application of mass timber in B.C.? How are professionals addressing these challenges?
Despite the growth of mass timber in B.C., technical barriers to broader application remain. A key challenge is scaling up domestic manufacturing capacity to meet growing demand across varied building types. While B.C. benefits from local sourcing, the mass timber industry still faces material cost volatility and logistical complexities related to supply co-ordination, particularly as adoption accelerates. Although U.S. trade policies introduce uncertainty for lumber exporters, developers building with Canadian-sourced mass timber for domestic use are largely insulated. Still, broader market dynamics, including competition for raw materials and evolving code requirements, continue to influence pricing, availability, and adoption timelines.
While B.C. has many innovative manufacturers, scaling up production to meet demand across diverse building types remains an ongoing challenge. To address this, the provincial government is investing millions into value-added lumber manufacturing—supporting projects such as advanced glulam production—to strengthen the local mass timber sector and build long-term capacity.
Code compliance also remains a hurdle. While B.C. has updated its building codes to allow mass timber buildings up to 18 storeys, navigating these regulations remains complex. Ongoing collaborative efforts by engineers, architects, and government bodies to modernize codes will likely address this barrier in the coming years.
What trends are emerging in hybrid structural systems (e.g. timber-steel-concrete composites) in B.C. mass timber projects?
Hybrid structural systems are emerging as a smart, sustainable solution for high-performance housing. By combining mass timber elements such as cross-laminated timber (CLT) floors with traditional stud-framed walls and conventional wood construction, this approach delivers strength, efficiency, and reduced environmental impact. A recent 118-home development in West Coquitlam showcases the potential of this method in action.
More broadly in B.C., the adoption of hybrid systems that blend timber with steel and concrete is gaining momentum. These systems capitalize on the unique strengths of each material to optimize structural efficiency, cost-effectiveness, and sustainability, while helping streamline permitting and code approvals.
Anything else you would like to add?
There’s a tremendous opportunity for B.C. to solidify its position as a leader in mass timber. Mass timber projects not only accelerate construction timelines and reduce greenhouse gas (GHG) emissions but also offer fire and seismic resilience. The integration of mass timber into building design supports human health, well-being and productivity—paving the way for a healthier, more sustainable future.