Stone adds a timeless quality to a Toronto landmark
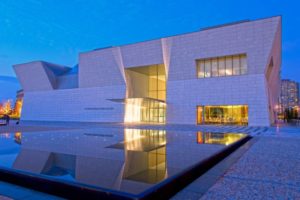
Photo © Tony Mo
by Michael Picco, P.Eng.
The Aga Khan Park in Toronto includes three distinct stone elements on a 7-ha (17-acre) campus-like property. The Aga Khan Museum and Ismaili Centre are light-coloured stone buildings. The space between them encompasses reflecting granite pools, and stone accents. A formal 1-ha (2.5-acre) garden connects the structures. The whole complex is a cultural hub and represents Canada’s vibrant diversity.
The $300-million campus was formally inaugurated on May 25, 2015. Approximately 8361 m2 (90,000 sf) of stone was employed in the project.
The Ismaili Centre
Designed by architect Charles Correa, the Ismaili Centre includes a place of prayer (jamatkhana) as well as spaces for social, educational, and cultural activities. The apex of the crystalline glass roof is the highest point on the property. Designed to illuminate the prayer hall, the domed roof incorporates a modern take on traditional Islamic architecture. Its frosted glass dome is framed by panes of translucent glass in a geometric star-like pattern, diffusing bright sunlight during the daytime while allowing the dome to glow from within in the evening.
The centre was initially designed to use concrete as its primary material. However, as the vision for the site expanded with the purchase of an adjacent property and the inclusion of a museum, it became apparent stone would be the most suitable cladding material because of its natural and timeless characteristics. The glass dome was originally going to be metal.
A light-coloured exterior reflecting spirituality was an important requirement. Therefore, a honed, cream-coloured Croatian limestone—high in luminosity—was employed. It has the ability to alter its appearance somewhat depending on the light it receives.
Aga Khan Museum
The main entry doors to the museum are purposely situated directly across from the centre of the glass roof of the Ismaili Centre. Inspired by principles of Islamic design, this precise alignment creates a sense of order, if only subconsciously, to bring a feeling of comfort and harmony to museum visitors. The client Imara (Wynford Drive) asked the design architect Fumihiko Maki to use “light” as his inspiration. In response, the architect decided to employ white, sand-blasted Brazilian granite to capture the changing aspects of daylight. This stone is rarely used for exterior cladding. It was selected because it displays a unique “life and flow” especially when wet due to the emerging swirls.
Formal garden
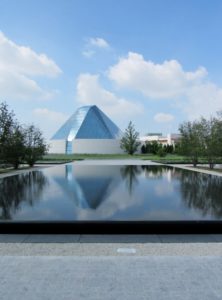
Photos © Sarah King
This green space, designed by architect Vladimir Djurovic, incorporates the concept of a char bagh or four-part formal garden with reflecting pools, pavers, planters, and benches. The five reflecting, infinity pools made from absolute black, polished Chinese granite, and situated 190 mm (7.5 in.) above grade, are the main focus. The dark colour maximizes reflection and is a contrast to the two lightly-coloured stone buildings at each end.
The beige and white, sand-blasted Chinese granite pavers, planters, and benches, systematically placed amongst gravel, connect the space and the two buildings. Carefully placed trees and shrubs augment the surroundings and add to the garden’s peaceful nature.
Stone selection
Toronto can possess a harsh climate in the winter. Freeze/thaw cycles over the many years of a building’s life and the effect of pollution levels from a nearby highway had to be considered. Granite was employed for the pavers because of the freeze/thaw cycles and salt exposure in the winter.
Notwithstanding the visits to various quarries across the globe, the stone selection process included numerous visits to Verona, Italy, where countless stone samples were prepared for viewing at the fabricator’s location. Once the stones were selected, several dry-lay exercises occurred including different preparations of the stone. These trips were sometimes combined with alternating visits to the site in Toronto to observe the possibilities under actual conditions. Additionally, extensive testing including freeze-thaw testing and absorption were performed on several stones.
Confronting the complexities and challenges
The shape of the Aga Khan Museum offered unique complexities and challenges. For example, the geometric shape of the building has an inward slant at the bottom, and outward slant at the top. The building has what can be described as a “seam” just over halfway up, which goes around the entire building. The slants in the façade (upward or downward) emanate from this seam.
It quickly became clear to the project team regular 90 degree stone panel joint lines (butt joints, quirks, and basic mitres) would not provide a clean, straight line as crisp and sharp as a custom architectural detail at the corners of the building. Therefore, a corner block detail manufactured from solid cubic stone was used. This served more than one purpose.
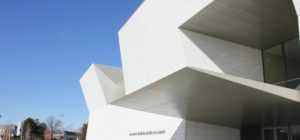
Firstly, the design smartly disguised the joints such that, when viewed up close, they were “hidden” in the recess folds. They are actually hidden within the shadows of the projecting sharp edge of the corner block when viewed at most angles.
Secondly, the design also facilitated the sharp crisp lines seen at a distance. This technique ensures the lines and edges of the building are perfectly straight and precise. This feature required special considerations in the anchor design at the corners to allow for three axis adjustment so as to facilitate absolute precision by the installers. Not only did the slanting demand perfection but any mistakes would be noticed immediately in the alignment of the horizontal joints.
One-, two-, and three-piece anchors were used on the museum. A 125 mm (5 in.) cavity was typical at all areas requiring insulation, and 50 mm (2 in.) stone thicknesses were the norm for the majority of the vertical surfaces. The stacked appearance of the slabs was meant to create the illusion the stone was heavier and thicker than it was. The pattern and dimension of the slabs also contributed to this effect. The lengths of the slabs range from 314 to 992 mm (12 to 39 in.). The heights are 314 to 442 mm (12 to 17 in.).
The precision was also noticed in some of the tolerances. For example, the installation of the stone was to a plane flatness and exposed end tolerance of 1.5 mm (0.05 in.) in 2400 mm (94 in.); variation in alignment from unit to adjacent unit was 1 mm (0.04 in.) maximum; and the variation of joint thickness was 1 mm every meter. Even the sealed joints were sprinkled with stone dust to cover joint sealants and provide indiscernible joints.
The Ismaili Centre slab sizes are:
- lengths: 584 to 672 mm (21.5 to 26 in.);
- heights: 594 to 897 mm (23 to 35 in.);
- thicknesses: 20 to 32 mm (0.78 to 1.2 in.).
The project team included Moriyama & Teshima Architects, Carillion Canada, PICCO Engineering, and Clifford Masonry.
Conclusion
As one walks around and experiences The Aga Khan Park, many thoughts and emotions are invoked. From the reflecting pools to the two stone buildings, the site with 8361 m2 of stone over slopped, curved, and multiplane surfaces is truly an oasis.
The author would like to thank Moriyama & Teshima Architects for their contributions to this article. For design resources related to natural stone, visit Natural Stone Institute and www.usenaturalstone.com.
Michael Picco, P.Eng., is CEO of PICCO Engineering. With 30 years of experience in natural stone cladding and structural engineering, Picco is an expert in stone sourcing and selection, consulting, manufacturing, installing, testing, designing, and detailing of stone anchors as well as shop drawings. Picco is an executive board member of the Natural Stone Institute (NSI). He can be reached at info@picco-engineering.com.