Specifying EPS as geofoam
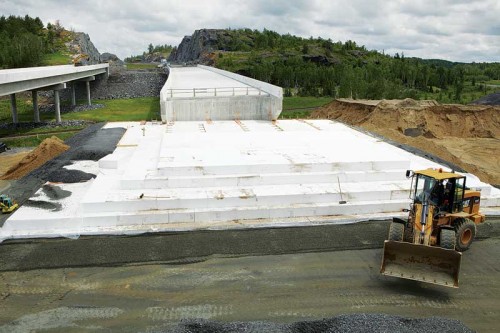
By W. James Whalen, P.Eng., MSCE, CSC
Moulded expanded polystyrene (EPS) is an air-filled, closed-cell, rigid foam plastic that does not contain any hydrochlorofluorocarbons (HCFCs) or hydrofluorocarbons (HFCs) as blowing agents. The closed-cell structure of EPS insulation provides constant thermal resistance, is dimensionally stable and non-corrosive, provides excellent mechanical properties, and can be recycled where facilities exist.
The generic term ‘geofoam’ is used to describe any synthetic geotechnical material created in an expansion process using a gas (i.e. blowing agent) and resulting in a texture of numerous closed cells. (See J.S. Horvath’s Geofoam Geosynthetic [Horvath Engineering, 1995]). Some typical EPS geofoam applications for buildings include:
- foundation wall insulation and drainage (e.g. the exterior below-grade wall);
- floor slab applications above or below concrete slab insulation;
- frost-protected shallow foundation (FPSF) insulation; and
- compressible inclusions—insulation and/or compressible material.
Non-building uses include:
- lightweight fill material for landscape applications;
- structural fill or insulation for road construction;
- insulation for underground utilities; and
- fill for earth-retaining structures.
The National Standard of Canada that addresses EPS insulation in building applications is Underwriters Laboratories of Canada (CAN/ULC) S701-11, Standard Specification for Thermal Insulation, Polystyrene, Boards, and Pipe Covering. Figure 1 provides the material properties for the three EPS insulation types included in CAN/ULC S701.
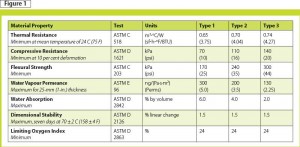
EPS geofoam applications require material performance properties beyond those specified in CAN/ULC S701. Figure 2 provides additional material properties for the three insulation types that may be used for design in EPS geofoam applications.
An additional industry standard often used for the material is ASTM D 6817, Standard Specification for Rigid Cellular Polystyrene Geofoam. Figure 3 summarizes the associated material properties for EPS geofoam types.
Performance properties
Some EPS geofoam performance properties that may be considered based on application requirements include:
- thermal resistance;
- compressive resistance;
- load reduction;
- moisture resistance;
- freeze-thaw resistance; and
- drainage capabilities.
Thermal resistance/thickness relationship
Thermal resistance value of an insulation material is stated as R-value or RSI; thermal resistivity is stated by R-value or RSI per unit of thickness. The R-value/RSI of insulation is a relative measure of the material’s ability to resist heat flow, with a higher R-value/RSI indicating a greater resistance to heat flow.
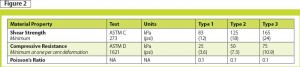
EPS insulation’s thermal resistance is closely related to the density of the finished product. Within the normal range of EPS densities, as the density increases, so too do the thermal resistance values.
LTTR
The major mechanism of heat transfer in foam plastic insulations is by conduction, which occurs through both the gas and solid portions of the foam. Since gases occupy approximately 90 to 98 per cent by volume of cellular plastics, conduction through the foam’s gas portion is by far the most significant.
Some cellular plastics depend on blowing agents (e.g. HFCs or HCFCs) inside their cellular structure to increase the thermal resistance value. However, since foam plastic insulations are not enclosed within gas-impermeable barriers, some of the blowing agent in the cellular structure diffuses out over time and is replaced by air, which has a lower thermal resistance value. This phenomenon is known as ‘thermal aging.’ Designers must request design thermal resistance values based on long-term thermal resistance (LTTR) test values to predict the insulation material’s performance for the life of the structure.
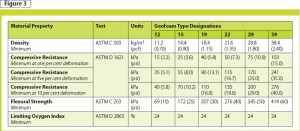
The Canadian thermal insulation industry has adopted a test method for predicting the design R-value of foam plastic insulations with a blowing agent within the cellular structure, and reporting of LTTR values is a requirement in current National Standards of Canada for foam plastic insulation. CAN/ULC S770, Determination of Long-term Thermal Resistance of Closed-cell Thermal Insulating Foams, is recognized as the test method for predicting the LTTR of closed-cell foam plastic insulation containing a gas other than air. It provides a means for predicting LTTR for foam plastic insulation with a captive blowing agent based on an accelerated laboratory test.
Since the closed cellular structure of EPS insulation contains only stabilized air, LTTR requirements are not applicable and the thermal resistance of EPS does not decrease with age. In other words, an EPS insulation’s published thermal resistance values are design values and do not require any adjustments for aging over the life of the structure.
Compressive resistance
Compressive resistance of foam plastics is determined using ASTM C 165, Standard Test Method for Measuring Compressive Properties of Thermal Insulations, or ASTM D 1621, Standard Test Method for Compressive Properties of Rigid Cellular Plastics. The value included in foam plastic insulation standards, including EPS, is the compressive stress at 10 per cent strain (deformation from original thickness) or yield, whichever comes first. This 10 per cent strain value is not a ‘failure strength,’ but rather is intended for product evaluations and quality control, as well as for comparing relative compressibility of different foam plastic insulations. The compressive resistance of EPS is closely related to product density.
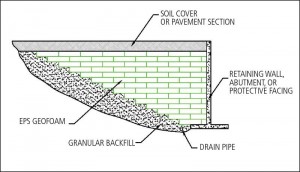
The compressive resistance at 10 per cent deformation should not be used for design purposes when EPS is subjected to short- or long-term compressive loads. If such compressive loads are anticipated, the compressive resistance at one per cent deformation is typically required for design purposes.
Moisture resistance
As EPS is a closed-cell foam plastic insulation, it resists the absorption of moisture into the cellular structure. Current foam plastic insulation standards specify maximum water absorption (percentage by volume) obtained from a laboratory test method. Maximum water absorption, specified in CAN/ULC-S701, is determined using ASTM D 2842, Test Method for Water Absorption of Rigid Cellular Plastics, which states the following under Section 2, “Significance and Use.”
The purpose of this test is to provide a means for comparing relative water absorption tendencies between different cellular plastics. It is intended for use in specifications, product evaluations, and quality control. It is applicable to specific end-use design requirements only to the extent that the end-use conditions are similar to the immersion period (normally 96 hours) and 5.1 cm (2 in.) head requirements of the test method.
There are now numerous published reports demonstrating that moisture resistance of EPS exposed in actual applications over extended periods is much lower than water absorption obtained from laboratory test methods. For example, a Finnish study comparing results from laboratory water absorption test methods to values from field applications found that actual water absorption in below-grade applications was less than half that predicted by laboratory test values. (See Oajnen et al’s “Moisture Performance Analysis of EPS Frost Insulation” in vol. 3 of the 1997 ASTM STP 1320, Insulation Materials–Testing and Applications). Similarly, a Norwegian report about EPS lightweight fill samples retrieved from applications after up to 40 years in service in a drained position found that moisture contents were less than one per cent by volume. (For more information, see Roald Aabøe’s “The Norwegian Public Roads Administration: 40 Years of Experience with the Use of EPS Geofoam Blocks in Road Construction,” which was part of the Proceedings of the 4th International Conference on Geofoam Blocks in Construction Applications, June 2011).