Brushing up on sustainability: Rethinking titanium dioxide in coatings
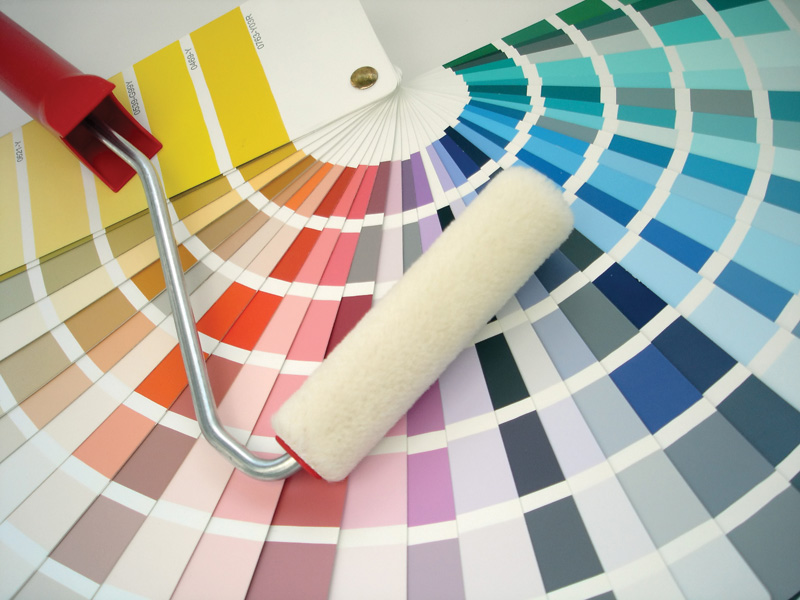
The coatings industry and its suppliers readily acknowledge the severe carbon footprint associated with titanium dioxide (TiO2) production. However, as their primary customer, the new construction and maintenance market shares an equal measure of this environmental responsibility. This interconnectedness has inadvertently driven both sectors into a precarious situation. But is there a viable escape route?
Architects, developers, and builders prioritize efficiency in their daily operations, generating business, managing resources, and serving clients. Consequently, they often overlook the profound impact of a single raw material, TiO2, on their ecological footprint, as highlighted by the Sustainable Paint Index.1 This impact extends beyond the coatings to encompass the labour and time involved in their extraction, production, supply, and application, regardless of economic conditions.
Since 1921, TiO2 remains the immutable material in paints and coatings. This naturally occurring, finite resource, provides unparalleled opacity—the essential whiteness and refractive index that defines paint’s hiding power. Yet, this very utility creates a paradox, contributing to both economic and environmental burdens through high production costs and an out-of-control carbon footprint.
Akzo Nobel’s 2017 exploration of a world without it revealed the challenge: significantly more coats (beyond the typical 2.5–3 using TiO2) were required using zinc (the average using zinc goes up to five coats), the next best alternative. Bound by traditional formulation design that struggles with diminishing returns, chemists can only increase its content so much before the cost-benefit ratio becomes unfeasible.
As the largest consumer of global paints and coatings, the construction and maintenance market accounts for more than 66 per cent of the industry’s total life-cycle waste, emissions, and carbon profile of society at large. While minimizing costs for better margins is a constant driver, it should ideally align with environmental considerations. However, aligning cost-saving measures with environmental considerations often means sacrificing either performance or maintaining affordable pricing.
The sustainability conversation once centred on volatile organic compound (VOC) limits—a concept that took a generation to permeate the construction industry yet yielded limited environmental benefit despite its relevance to human health. Today, the focus has shifted to CO2 footprint and waste reduction, resonating with an increasingly informed consumer base that demands tangible and quantifiable environmental action from the products they purchase. This directly influences how the construction sector procures and uses coatings for their clients.
In today’s landscape, costs are inextricably linked to carbon emissions and waste footprint as much as to supply-side economics. Both are fundamentally determined by the number of coats or gallons required and the opacity or hiding power provided by TiO2. Controlling the number of coats or gallons means controlling both economic and environmental costs. Achieving this, however, requires gaining control over this pivotal material.
TiO2: The linchpin of sustainability in construction coatings
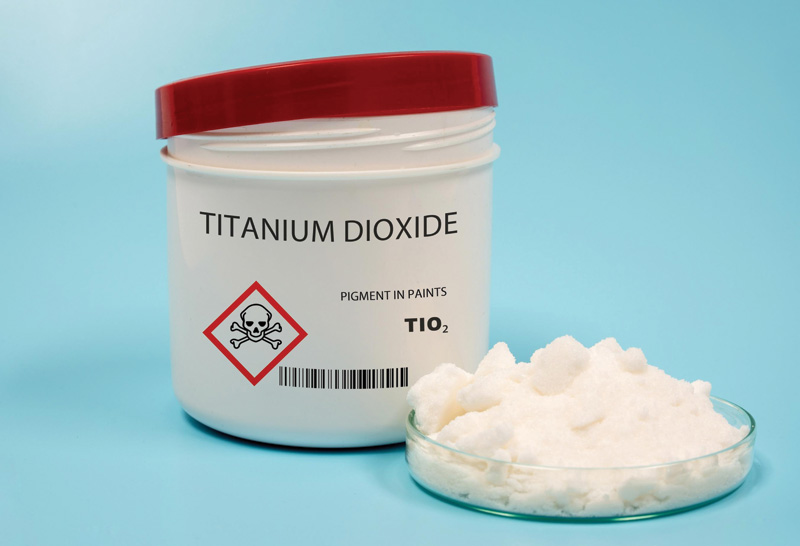
A groundbreaking sustainable construction technology, leveraging advanced light scattering and optimized TiO₂ usage, offers a novel universal coatings system for diverse substrates and market segments—potentially resolving a critical industry dilemma. This method, termed “Self-Build Technology,” maximizes the efficiency of paint’s core function: opacity, upon which all other performance benefits depend.
Insufficient opacity detrimentally affects peripheral benefits such as UV resistance, adhesion, washability, moisture resistance, colour retention, and gloss level. The need to “paint another coat” is more than just a minor inconvenience; it reflects fundamental limitations in how coatings perform in real-world conditions. Application variables such as user skill, tools,
and the number of coats applied directly influence how well a coating adheres, how durable it is, and how consistently it delivers colour or gloss. No other function is more universally tied to performance, cost, and reliability across all markets and coating sectors than opacity.
Interestingly, while the industry acknowledges the challenge of optimizing TiO₂, it often overlooks its core value because traditional formulations cannot solve the opacity issue directly. This innovation changes that. Through a unique “mechanism of action,” which allows paint molecules to self-assemble in real time like Lego bricks during standard application, yielding equivalent performance from thinner film build thickness (and all other desired properties) of multiple coats from traditional coatings, but without the need of a primer or a second coat and with significantly greater durability. The technology uses “thin film building” as it does not rely on heavy, thick coats to function, but the film build result is equivalent to multiple coats and not thinner.
The underlying concept poses a simple yet profound question: “If conclusive opacity, the visual queue to stop painting, is currently achieved through multiple coats applied sequentially over time, how can these layers, and therefore the complete result, be achieved instantaneously during a single application?”
This idea draws inspiration from the optical behaviour of sodium chloride (NaCl). In its static form, NaCl is transparent. However, when many grains are clustered together (mechanism of action), they become opaque, effectively scattering light. Remarkably, although TiO2 boasts a significantly higher refractive index (2.61 versus 1.54 for NaCl), traditional coatings still require multiple layers to achieve complete opacity.
This innovative approach reaches opacity through thin film building, where paint molecules adhere to the substrate and each other, capitalizing on refined surface tension principles. This is achieved during production through a controlled shearing effect, “magnetizing” paint molecules through specific treatment and sequencing of raw materials within each chemical component. Despite this distinctive outcome, the system uses 90 per cent of the same raw materials and standard equipment manufacturers use globally. This method yields three times the opacity of traditional architectural construction coatings, using two-thirds less TiO2.
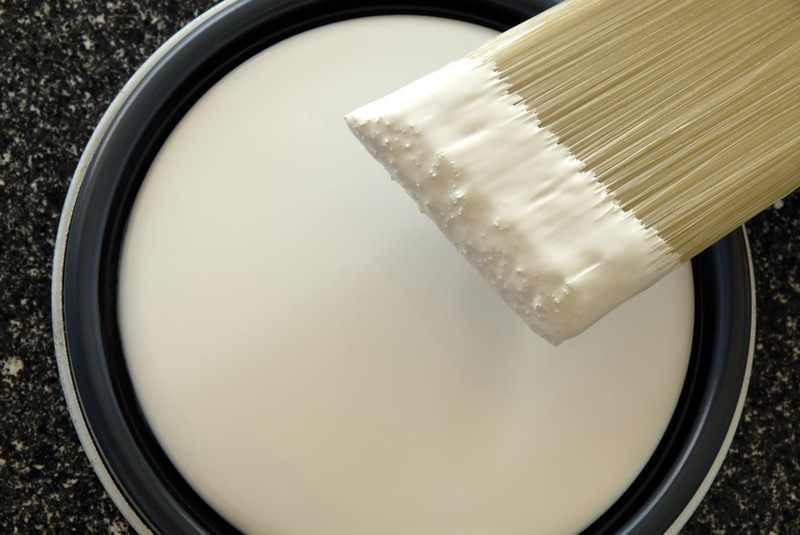
While traditional coatings excel at surface adhesion, they often shift and move before drying, leading to an incomplete finish that necessitates multiple layers/gallons to achieve opacity and, subsequently, all other desired properties, such as sheen, texture, colour, and durability. This reliance on layering is the established hallmark. Critically, opacity remains the only uncontrollable aspect of a coating’s performance, as current techniques and methods in formulation cannot tame it.
With TiO2 emerging as an environmental concern, its reduction seems inevitable. The EU is considering bans, while some producers, such as Chemours, acknowledge its systemic impact, subtly encouraging reduced consumption. Resin suppliers, such as Arkema, are also exploring long-term alternatives through stakeholder conferences. Meanwhile, global trade dynamics, such as China’s anti-dumping tariffs, add further instability that spirals a global industry and customer base.
Publicly, this signals that simply banning TiO2 without a viable alternative would likely exacerbate the problem. This would lead to increased material consumption to compensate for reduced opacity, further burdening the production infrastructure and supply chain. Without a new formulation paradigm, manufacturers will continue to purchase more TiO2 and pass their limitations onto construction and its customers, perpetuating a less sustainable system that affects national and global markets.
To remain competitive, construction requires a more responsible approach to both business and the environment. Current standards inadvertently position TiO2 as an adversary when it could become a valuable ally, enabling genuine control over the environmental footprint while encouraging economic growth.
The implications of construction gaining control over this systemic issue extend far beyond a single raw material. By effectively optimizing TiO2 use and consumption, the industry can inherently control the demand for all material inputs to serve its function. Just as planets orbit the sun, peripheral materials such as additives, resins, water, fillers, energy, transport, and packaging will naturally reduce to their minimum required levels. This is the profound power of this control: the ability to shrink supply chain consumption across the board and prevent maximum life-cycle waste from the outset. This represents the only path to sustainability when using all coatings.
Achieving this goal allows the coatings industry to offer the construction sector a significantly minimized eco-footprint as a tangible benefit, nurturing a new era of environmental stewardship. Customers should not be expected to pay a premium for eco-friendliness; rather, the responsibility lies in innovating apex solutions that deliver environmental benefits while increasing economic viability. This genuine integration is the only way forward and acts as a double incentive model to perpetuate its success.
Echoing the sustainability messaging of leading manufacturers, who aim to “detach growth from environmental footprint,” the reality remains that the most environmentally friendly coating is used least. However, the current global market lacks a readily available paint product portfolio that supports this aspiration.
This concept aligns with the principles of extended producer responsibility systems (EPRS), initially conceived by governments to curb post-consumer waste. While EPRS evolved into a manufacturer-led initiative funded by consumer eco-fees for recycling Self-Build Technology and its control over TiO2 and, therefore, the entire footprint of the construction industry can revive a somewhat forgotten inclination to control waste at the source—from the point of raw material extraction.
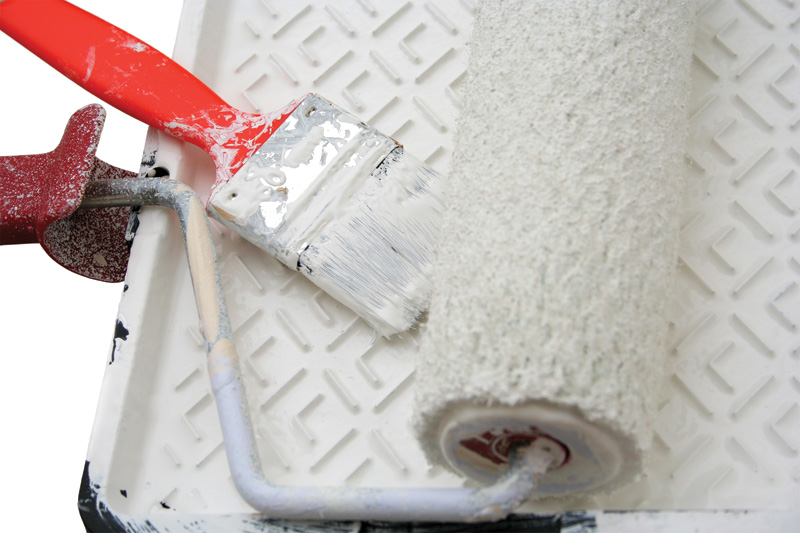
A paradigm shift: From uncontrolled waste to total control
The table on page 10 illustrates the fundamental difference between the current life-cycle system and this proposed novel system where the construction sector leverages its influence to drive real change in coatings consumption back up the chain.
As illustrated in the table, the proposed system minimizes all waste across the supply/value chain: raw material extraction, finished goods production, containers, transport, energy, water, CO2/GHG emissions, and recycling infrastructure limitations.
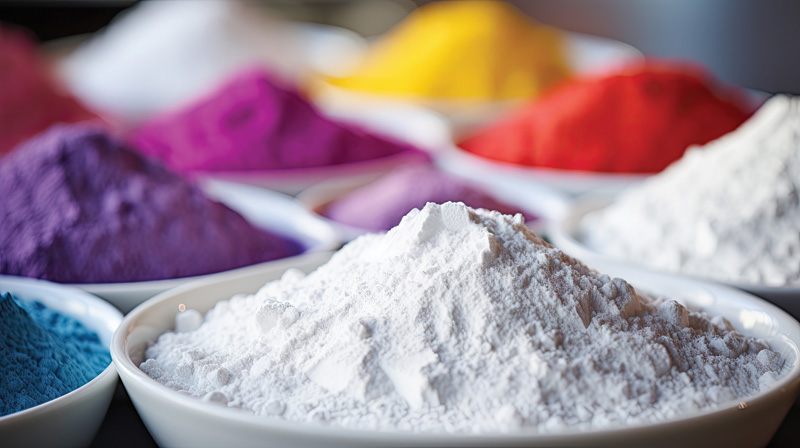
Moving beyond symbolic gestures
How does the industry achieve genuine, quantifiable environmental change? While initiatives such as planting trees, carbon capture post-generation, and encouraging cycling, in principle, feel good and are esthetically correct, these are reactionary notions benign of any significant consequence. If the construction industry’s commitment to sustainability is as strong as it claims, consider the transformative power of every architect, developer, and builder adopting this novel system. What would be the national and global impact? For generations, marketing has convinced people that fewer coats are desirable and common sense, yet current market products have not made this a reality.
This construction technology would immediately reduce global TiO2 consumption from 50 per cent of feedstocks to just 17 per cent. This, in turn, would maximize the preservation of peripheral resources and permanently minimize the CO2 footprint and all excess input costs throughout the entire supply chain.
This paves the way for genuine climate-tech coatings, the foundation for true environmental, social, and governance (ESG) principles, addressing global sustainability megatrends. This approach is rooted not in superficial marketing but in the fundamental purpose of paints and coatings production. Ultimately, this empowers consumers and defines construction’s true participation and responsibility within a renewed system.
Currently, the construction industry is constrained by its reliance on TiO2 while facing increasing pressure from consumers, environmental agencies, and innovators. Progress will remain inhibited unless a real-world alternative offering a dual economic and environmental incentive, as proposed here, is embraced.
The irony for construction is that, in this instance, bigger is not synonymous with better. The more development is undertaken, the greater the environmental responsibility. If the coatings and construction sectors fail to optimize TiO2 usage and bring innovative solutions to fruition, significantly altering the current unsustainable trajectory will be challenging, making it difficult to justify the continued operation of two of the world’s most wasteful and expensive supply chains to the mainstream consumer.
In conclusion, refer to George Pilcher’s “Transformational thinking” paper from the October 2012 European Coatings Journal article, “Innovating for the future.” Pilcher highlights that paints and coatings, aside from the shift from oil to latex in the 1950s, have seen little fundamental change in a century—a timeline that coincides with the widespread adoption of refined TiO2. The paper argues that true innovation requires transformational thinking, a spark that fundamentally alters our perception of coatings and the processes through which they are applied. It is crucial to steer clear of gradualism and embrace a conversion to recalibrate the relationship between the coatings industry and its most prominent user, thereby empowering the construction and maintenance markets to lead the way for all stakeholders.
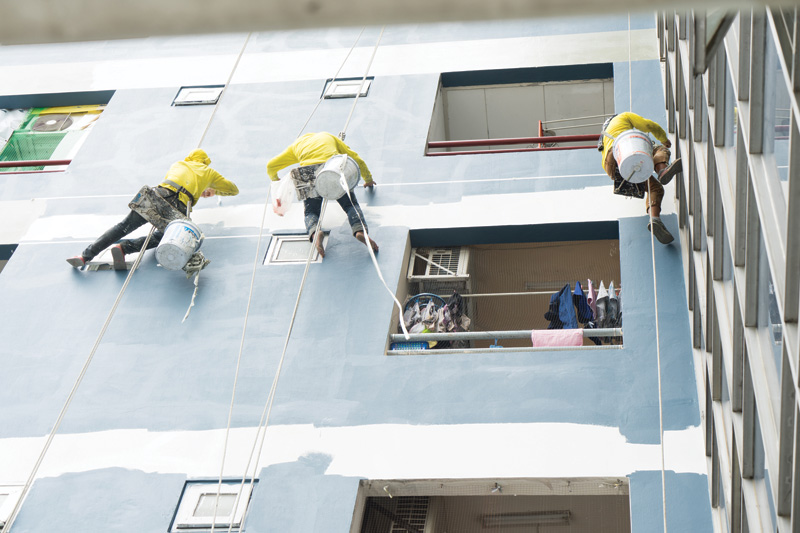
Notes
1 Learn more about the Sustainable Paint Index at constructioncanada.net/sustainable-paint-index-a-shift-in-architectural-coatings/
2 While it is possible to mainstream the use, the process is synthetic, and the author is referring to offsets. No lab-created material (synthetics), such as pre-composite polymers, can replace the effectiveness of TiO2, which is naturally occurring. In 2011, Dow Chemical launched “Evoque,” a polymer that won the EPA Green Chemistry Award that year. In 15 years, it has successfully offset only 7 per cent TiO2 in a standard paint and coating formulation.
Category | Current system: Uncontrollable chain reaction in economy and environment | Proposed system: Total control through reduced consumption |
System characteristics | Maximum waste recycling infrastructure and CO2e/GHG emission generation.No control of the system using the second and third “R” (reuse/recycle). |
Total control with 66 per cent reduced TiO2 means 66 per cent reduced consumption through the supply chain and maximum reduced Scope 1, 2, 3 emissions.
Achieved through the principle |
Coats and coverage | Two-and-a-half to three coats average. The general measure is one coat to a gallon, which averages 33 m² (350 sf) of paintable space. The average DIY paint job is a purchase of 12 L (3 gal) or 100 m² (1,076 sf). |
Eliminating the primer and second coat through Self-Build Technology. |
Raw material stage | Raw material suppliers extract and supply inherently limiting natural resources in opacity, such as TiO2 with no synthetic counterpart, initiating excessive life-cycle waste and CO2e/GHG emissions. | Reduce TiO2 extraction, which reduces all other material inputs through production and supply through to the end user. |
Manufacturing stage | Manufacturers overproduce due to opacity limitations, compounding waste, and CO2e/GHG per gallon. |
Optimize opacity, the core utility of coatings. |
Regulatory and association impact | Coatings associations charge “eco-taxes” to fund fledgling recycling infrastructure to manage their image, further compounding life-cycle impacts as, ironically, recycling requires waste generation to be successful. | (Not directly applicable in proposed list, but implicitly addressed through reduction strategy.) |
Users/construction/maintenance stage | Users/construction/maintenance generate significant annual “post-production and use waste” (16 per cent of production/860M litres in North America), CO2e/GHG per gallon at this stage hits 18 kg (40 lb). |
To control the number of coats is to control costs, minimizing labour, time, materials. |
Recycling and end-of-life | Paint and product care recapture an insignificant 0.3 per cent of annual waste for reuse. No demand for recycled products leads to repeated costly processes and eventual landfill disposal, continuously compounding waste and CO2e/GHG emissions. | Control of eco-effects—Maximum possible prevented CO2e/wastes means detaching growth from footprint. |
Overall outcome | Excessive life-cycle waste, carbon footprint, and inefficiency throughout the value chain. | This minimizes all waste across the supply/value chain: raw material extraction, finished goods production, containers, transport, energy, water, CO2e/GHG emissions, Scope 1,2,3, and recycling infrastructure limitations. |
Author
Tonino F. Margani is a fourth-generation painter in Toronto and the EVP of science and environment for Nobilis Inc., a family office in the research and commercialization of global paints and coatings.