Layered logic: The case for rainscreens
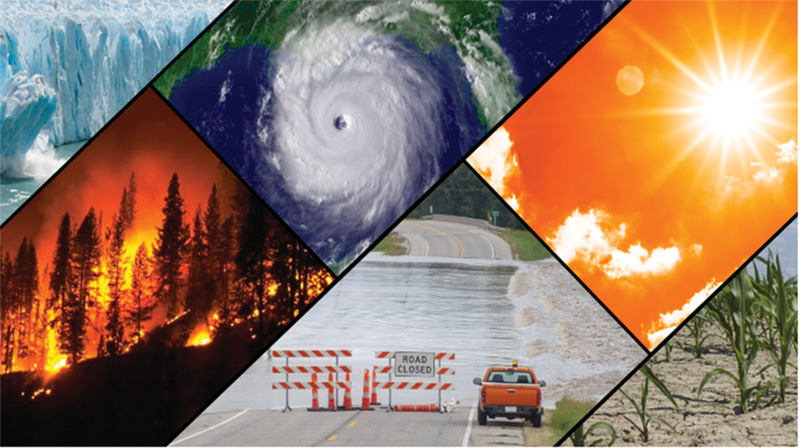
In the context of North America’s diverse climate, rainscreen facades are considered to be one of the most practical and effective solutions for exterior wall design. Despite being a well-established technology, many buildings still lack the benefits of this advanced facade performance. This raises the questions: why, when, and where is a rainscreen the right choice? Water wins. That statement is often well understood in the world of construction. This is much like a rock/paper/scissors game. There is an order of dominance in the shapes vis-à-vis one another, but no one symbol dominates all. If water were included, it would win every time. Whenever considering the healthy structural integrity of a building, it typically does not include moisture in the mix. A humidity range of 30 to 50 per cent is beneficial for general health, but in construction, water permeation is typically frowned upon.
The evolution of building envelopes
The function of a building envelope is to separate the exterior environment from that of the interior. Traditionally, this includes separating thermal conditions, precipitation, and wind. Precipitation was traditionally thought to be managed with what is currently referred to as a perfect barrier, comprised of either masonry or wood. In contemporary designs, it could be expanded to metal, vinyl, or stucco (EIFS). The idea of the perfect barrier was that it possessed no flaws to permit moisture intrusion. And if it remained ‘perfect,’ it would succeed at this. The problem was, even if these barriers started out perfect, they seldom remained so. They would eventually develop flaws, and moisture would infiltrate without a sufficient means to escape before damage resulted.
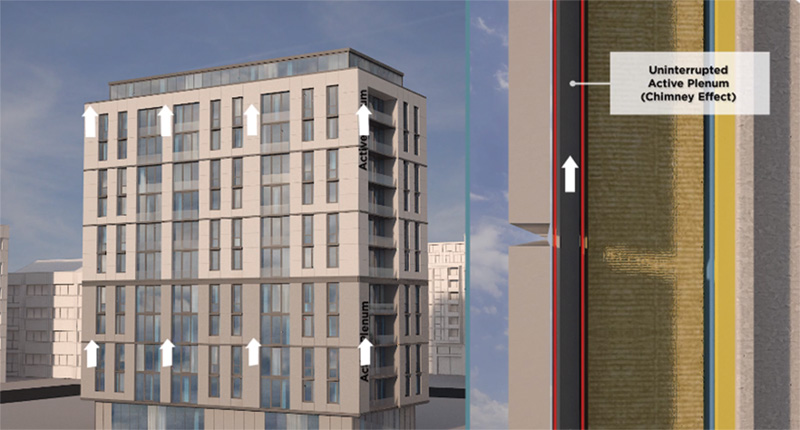
Why imperfection works
An imperfect barrier, despite its name, has the potential of being a far more effective system than it sounds. In the world of facade technology, an imperfect barrier system is made up of a combination of barriers. Not one of the single barriers is tasked with completely stopping moisture intrusion. It uses a layering system and diminishes the precipitation/moisture as it attempts to transcend through multiple layers of the facade. In a sense, it is like a combination of hurdles that restrain the inward movement of precipitation through the system, until the water runs out of momentum and falls on its face. It is also vented and drained through an unobstructed active plenum. Venting ultimately absorbs and exhausts the remaining moisture that gravity could not drain. It should be noted that not all moisture found within a wall cavity is the result of precipitation, but could be the result of condensation from thermal deltas. Moisture within wall assemblies, regardless of origin, needs to be evacuated.
While the outermost layer has to manage the punishment of UV stress, wind, and other environmental stressors, the inner barriers do not. As a result, their lifespan is far greater. The outermost layer, if required, can be replaced with relative ease without disrupting the remainder of the inner system, and the envelope can remain intact. A rainscreen is an imperfectly ‘perfect system’ in this context. One could describe it as giving precipitation a front door to enter and a back door to exit.
The wondrous quality about high-performance rainscreen technology is that there is never a circumstance where it is the wrong solution for a facade system. Some environments can justify it more than others, but it is never less than a great design. It can also be made of a multitude of materials. Some materials will endure better than others when confronted with environmental stressors (UV, wind, freeze/thaw), but it is all about the how and virtually nothing about the what. Metals, fibre-reinforced composites (FRCs), ceramics, and phenolics are among a few materials that traditionally make up a contemporary rainscreen. Some of these materials require rainscreens to meet their respective warranty requirements. The materials are the outer skin of the assembly or the ‘armour.’ Rainscreens manage moisture well and conveniently work in unison with outboard insulated high-performance facade systems. This makes a rainscreen a relevant and passive technology when considering the higher thermal performance the building industry strives for, whether in a cold, temperate, or warm climate. Lastly, the successful management of wall assembly moisture that rainscreens offer also has beneficial implications for the health of occupants.
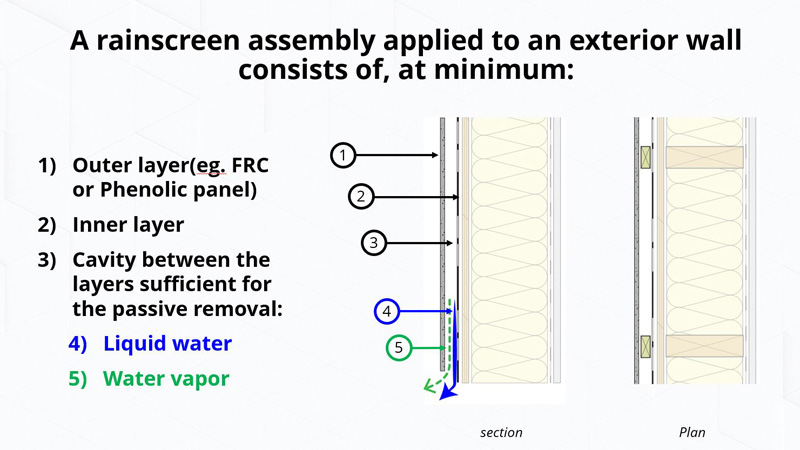
The role of RAiNA
In 2020, an association named Rainscreens in North America (RAiNA) was founded. The founding members appreciated the benefits of rainscreen technology and, through empirical building science-based expertise, were determined to share it with their industry peers. At the time, this technology had some roots in Canada, fewer in the U.S., and less in Mexico. One of its primary focuses was establishing a single and current design definition for rainscreen, as there were now many in the current industry and many of those that had evolved proved less effective than others. RAiNA arrived at this: “A rainscreen is defined as an assembly applied to an exterior wall which consists of, at minimum, an outer layer, an inner layer, and a cavity between them sufficient for the passive removal of liquid water and water vapor.”

Since its inception, the association has opened itself to membership and invested in creating various committees to address technological questions, establish a vocabulary, develop specifications, etc. The RAiNA mandate is to be the authority on rainscreen wall assemblies in North America, and they pursue this relentlessly. Through this focus, they provide educational tools, conferences, and technical material for the industry to rely on as a guide for integrating this technology into the current design of new buildings and retrofits. Given some of the poor design iterations of rainscreens in the past 30 years, this association and initiative come at a good time, as the technology, applied correctly, is very successful.
New builds, retrofit, and economic realities
New buildings can be designed with a high-performance rainscreen facade, and many are. The question remains: Why are all new buildings not adopting a rainscreen-type facade? While there is no simple answer to this, there is a lingering resistance to change in the construction industry. The adage of “why can’t we do it the way we’ve always done it” continues to hinder innovation. Truth be told, Southeast California, Nevada, and Arizona do not see precipitation to any significant degree and would not suffer noticeably if rainscreen technology was not employed in these areas. Yet, it could be employed, and would not add any remote degree of significant costs to any cladding project. For that matter, buildings in the Middle East would be fine building their envelopes in their traditional manner as well. Though all of Europe, most of the Americas, Australia, Oceania, and Asia should be building with a rainscreen design. Rainscreen technology is smart technology and planning for the future often involves accepting change, not resisting it.
There is also the potential to incorporate rainscreens in retrofit scenarios. Repurposing buildings is a large market in recent years, and recladding a building for rebranding purposes, or for amping up thermal performance with outboard continuous insulation (c.i.), is an obvious opportunity for rainscreen technology. So, while rainscreens are an innovative facade design and there is never a geographical or climatic circumstance where it is the wrong solution, does that mean the industry will be retrofitting all buildings without rainscreens to have one? Probably not. In most cases, where a particular building could perform better, though there are no apparent signs of deterioration, no owner/operator will typically spend significant money to upgrade the facade when it does not appear to be compromising anyone. Then there are cases where a reclad is in order, but the process is prohibitive because the existing structure lacks the integrity to support a new one. This is common with brick buildings, for example, where masonry is in poor condition or brick ties are deteriorated. Some cases cannot be helped.
A new standard
An effective high-performance rainscreen benefits a building tremendously in managing unwanted moisture. The contemporary facade should be engineered with high performance in mind, as it is the armour of the primary passive environmental control system of a building. As the industry moves toward pushing the envelope of better building science, there is a need to ensure the best technology at hand is being employed for new builds and applicable retrofits, because rainscreens are affordable and effective. So the question is, can the industry afford not to build with rainscreens and make them the new standard? The answer is that it cannot.
Author
Jeff Ker is the senior technical advisor at Engineered Assemblies. He has more than 30 years of technical sales experience within the Canadian architectural and construction community, 14 of which were spent specifically representing a variety of high-performance rainscreen systems.