Managing stormwater with bioretention low impact development systems
Overcoming design challenges
Bioretention systems are best placed in areas that promote infiltration, unless otherwise specified by the design practitioner. The elements one ought to look for when siting a bioretention system include well draining soils and sufficient separation from groundwater and bedrock. These factors allow bioretention systems to drain through infiltration. Options can still exist where site conditions are not ideal.
For sites that have soils with low infiltration rates, subdrains can help prevent the bioretention system from becoming water-logged. Bioretention systems typically have stone layer between 0.3 and 1 m (1 and 3 ft) deep at the bottom of the system. Depending on the design, these subdrains may be located either at the bottom of the stone layer, so that all the runoff entering the system drains out through the subdrains, or be placed at the top of the stone layer, enabling a portion of the runoff to infiltrate. If subdrains are used, the design should specify a geotextile surrounding the stone layer or a filter sock around the subdrain to mitigate the system clogging.
For sites with shallow groundwater, a clay or synthetic liner can help prevent the filter media from becoming water-logged. Depending on the size of the system, the installation of this liner may need to be supervised by the site geotechnical engineer. Lined bioretention systems must include both a subdrain and an overflow outlet, so they drain between rainfall events. The plants in lined systems must be carefully selected, so root systems do not damage the liner. If plant substitutions are needed, they should be approved by the system designer.

For sites with shallow bedrock, the construction challenges include both low infiltration rates and excavating around bedrock. Bioretention systems installed on sites with shallow bedrock could be designed with shallower stone and filter media layers. If the bedrock is fissured, a liner may be needed to keep enough water in the bioretention system to support the plants. If the bedrock is solid, a subdrain and overflow will be needed for the system to drain between rainfalls. Plants used in shallow bioretention systems must tolerate having shallow root systems. Any necessary substitutions should also be approved by the system designer to ensure the plants can thrive.
The requirement for LID systems in many jurisdictions lead designers to feel pressured to design bioretention systems in less-than-ideal locations. However, bioretention systems can be specified with a few design modifications to work on sites with low infiltration rates, or those with shallow groundwater or bedrock.
Communicating these design modifications to the construction team enables designers, contract administrators, site inspectors, and contractors to understand the design and be aware of the potential challenges when building a modified bioretention system. With innovative design and good communication within the project team and those in the field, bioretention systems can work well for years, even on sites with unfavourable conditions.
Construction challenges influencing bioretention performance
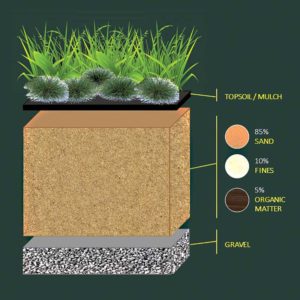
The industry is learning to alleviate some of the challenges of installing bioretention systems by improving communications, enhancing specifications, and working together. When designers, contract administrators, and contractors work collaboratively from the design and specification stage all the way through final certification, it results in improved long-term performance of the bioretention system.
When preparing the tender documents, all design practitioners—including civil engineers, landscape architects, and geotechnical engineers—should not only discuss the specifications for the bioretention system and its components, but also the staging necessary for a bioretention system. Before any site work begins, the area of the bioretention system must be protected with erosion and sediment control measures to avoid sediment clogging the native soil or the construction activity compacting it. If earthworks are happening onsite, the bioretention system area must be filled with high permeability soils, which may need to be imported and placed in these areas. All trades onsite, including building and utility trades, should be aware of the bioretention system, so they do not inadvertently compact or otherwise damage the area after it has been landscaped and appears as a regular landscaped area.
Communication between all parties is also important when adapting to field conditions. Although every effort may be taken to have records of existing infrastructure and sub-surface soil conditions during the siting and design stage of the project, actual site conditions could be different or change once construction begins. Open communication and problem solving is imperative at this stage to minimize impacts to both costs and schedules.
Table 1 – Bioretention System Design Guidelines
Design Guidelines | Description |
General Information of Bioretention Systems | |
Sustainable Technologies Evaluation Program (STEP) | This program is a multi-agency initiative developed to support broader implementation of sustainable technologies and practices within a Canadian context. |
STEP Low Impact Development WIKI | This website contains information on low impact development. Although managed by STEP, this site allows users to edit content; therefore, please verify information found on this website before implementing it in a design.
https://wiki.sustainabletechnologies.ca/wiki/Main_Page |
Design and Planning Guides for Bioretention Systems | |
CSA W200-2018
Design Of Bioretention Systems, CSA Group, 2018 |
CSA Group has developed a standard for the design of bioretention systems in compliance with the Standards Council of Canada. This standard provides recommendations for the design of bioretention systems intended for the management of urban stormwater runoff. |
Stormwater Management Planning and Design Guide, Ontario Ministry of the Environment, 2003 | The Ontario Ministry of the Environment, Conservation, and Parks (formally Ministry of the Environment) is the final approval agency for stormwater infrastructure in Ontario. This manual is the foundation most of the agency’s design guidelines are based. |
Low Impact Development Stormwater Management Planning and Design Guide,
Credit Valley Conservation (CVC) and Toronto and Region Conservation Authority, 2010 (Now found on the STEP website) |
A guide for designers who want to implement low impact development practices, it includes information on the design of many low impact development (LID) techniques, including bioretention systems. This guide also includes how to integrate LID systems into a design starting from the early planning stages of a development. |
Fact Sheet on Low Impact Development Stormwater Management Planning and Design Guide – Bioretention
Credit Valley Conservation and Toronto and Region Conservation Authority, 2010 |
This fact sheet provides a useful summary of the design of bioretention systems. A fact sheet has been developed for each low impact development (LID) system which now can be found on the STEP website. |
Construction and Inspection of Bioretention Systems | |
Low Impact Development Certification Protocols: Bioretention Practices
Credit Valley Conservation, 2017 |
This guide help municipalities and private landowners in Ontario formalize a system for certifying low impact development (LID) systems after they are constructed. LID systems are mostly underground and, therefore, operation and maintenance personnel need a procedure to ensure the systems are working as specified. |
Low Impact Development Construction Guide,
Credit Valley Conservation, 2012 |
The Low Impact Development (LID) Construction Guide bridges the gap between the design and construction of LID systems. Written for design consultants, municipal engineers, plan reviewers, and construction project managers, this guide highlights common LID construction failures and how to avoid them. |
Contractor’s & Inspector’s Guide for Low Impact Development,Credit Valley Conservation, 2014 |
This guide complements the CVC Low Impact Development Construction Guide (2012). Contractors and inspectors can use this guide daily to ensure LID projects are installed properly through all phases of the project. |
Low Impact Development Stormwater Management Practice Inspection and Maintenance Guide
Toronto and Region Conservation Authority, 2016 |
Municipalities and property managers in Ontario can use this guidance document to design an effective inspection and maintenance program for low impact development (LID) systems. |
Inspection and Maintenance of Stormwater Best Management Practices—Fact Sheet – Bioretention Toronto and Region Conservation Authority, 2016 | This fact sheet summarizes the inspection and maintenance practices for bioretention facilities along with cost estimates for common maintenance activities. Similar fact sheets are also available for other low impact development (LID) practices on the STEP website. |