Designing EPCOR Tower
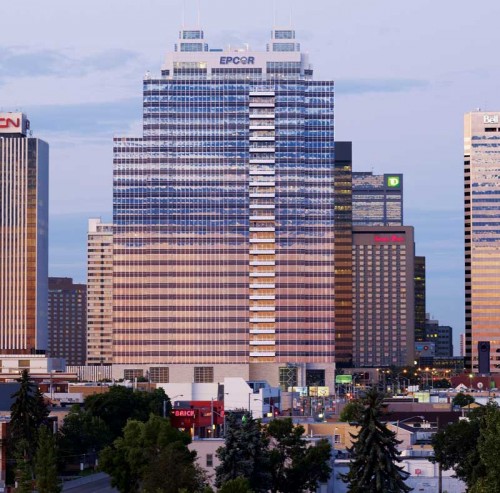
By Honor Morris, BA, Christiaan Odinga, BFA, BArch, MRAIC, and Ken Cantor
In the September 2011 issue of Construction Canada, the authors examined some of the basic design concepts behind EPCOR Tower—the first multi-storey office complex to be constructed in Edmonton in 20 years. This second article goes into more depth regarding the various elements and processes.
Construction on EPCOR Tower began in March 2008. The need to secure a reliable and experienced construction team was of paramount importance and the major trade contractors were assigned to the project within the first three months of an aggressive 3.5-year construction schedule.
Due to the project size and limited local experience in this building genre, there was only a select pool of trade contractors that could complete the development from a manpower, knowledge, and schedule perspective.
Excavation and shoring
The overall site for the EPCOR Tower extends beyond the footprint of the building. Six and a half months before the commencement of the excavation process, Alberta Environment revised some of the existing criteria and policies linked to the definition of “contaminated soil.” This resulted in some of the soils on the site previously classed as “clean” to be reclassified as “slightly impacted.”
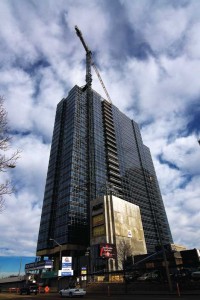
Photo © Ken Cantor
The excavator contractor’s environmental consultant then evaluated the available options. He recommended approximately 10 per cent of the 35,000 m³ (376,735 cf) of ‘impacted’ material be transported to a landfill site. The remaining 90 per cent—284,750 m³ (3,065,025 cf)—was available to be used at other suitable locations within the city after additional segregation and testing was undertaken. This strategy ultimately saved the developers hundreds of thousands of dollars and also diverted substantial quantities of material away from the landfill site.
The shoring element of the construction process incorporated approximately 4550 m (14,930 ft) of W530 and W610 steel soldier piles. The 250 soldier piles have an average depth of 18.2 m (60 ft). The parkade structure is effectively constructed on a zero-lot line basis on the north and south property lines, and near the 101st Street property line to the west. This condition and the depth of the four-storey underground parkade required the use of 820 grouted tie-backs.
Rebar and concrete
EPCOR Tower is a conventional cast-in-place concrete structure. The fly ash quantities are 50 per cent by mass of the total cementing material for many of the elements, including footings and columns. The horizontal elements have the more typical fly ash replacement of 25 to 30 per cent, to allow for rapid stripping of formwork. Concrete strengths are varied to reflect seasonal construction requirements as well as design criteria.
Parkade floors were designed to maximize the benefits of a proprietary forming system. Their 300-mm (11.8-in.) thick slabs were constructed without drops except where high mechanical plant and storage loads were expected. By locating floor drains at mid spans, the need for control of the slab camber was negated.
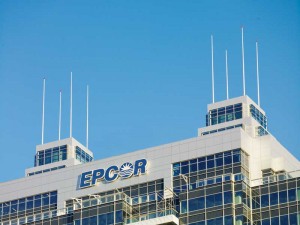
Photo © Ian Grant
The tower’s above-grade portions comprise slabs and band beams spaced to match the 9.1-m (30-ft) column spacing. Each beam cantilevers from 2 to 3.5 m (6.5 to 11.5 ft), providing for the construction of an unobstructed glass face. A structural steel option was considered, but the nature of the exterior cantilevers made this alternative less advantageous. Above the occupied floors, the building’s crowns are constructed with galvanized steel, to allow for internal lighting of the open glazed structure.
Floor load capacities greater than code minimums were provided to ensure flexibility in office layouts and to permit some tenants to incorporate raised floors. Consideration was given to designing some floor areas to even higher loads, such as around the cores or to meet specific tenant requirements.
The footing and raft foundations for the tower are somewhat unusual in that they are founded 18 m (59 ft) below grade at their deepest, although not solely to accommodate the four-storey below-grade parkade. The site was purchased with an existing easement, held by the City of Edmonton, for a light rail transit (LRT) tunnel. As the design progressed, it became apparent the LRT tunnel would have an impact on the tower column footings and vice versa.
The proximity of the tunnel to the tower columns required separation of the very heavy tower from the relatively light adjacent LRT cavity, which would typically be prone to heave. By dropping the raft foundation, separating the two structures, and placing the north columns on an extension of the 2.3-m (7.5-ft) thick core raft foundation, it was possible for both structures to independently progress (and settle).
Thurber Engineering, the geotechnical consultant, modelled the deep layers of clay, interbedded sand, and clay shale. It predicted approximately 40 mm (1.5 in.) of settlement for the tower foundations. Although the adjacent LRT tunnel carries two rows of parkade columns, the size and timing of the cavity was such that little to no movement was predicted. The use of pour strips around the tower structure allowed this differential settlement to occur in a relatively stress-free manner. While the result was the creation of a sub-parkade void and an extra level of structure to the tower, this space became useful following some value engineering reviews.
The mechanical design team indicated a preconditioned air supply would be of benefit for tower ventilation, and the structural team proceeded to design a large earth tube. Heat transfer is augmented by small closely spaced column ‘fins’ in the 9-m (29.5-ft) wide cavity above the tower raft. This design allows the earth tube to become thermally connected to the deep soil mass for both pre-cooling and pre-warming ventilation air.
A second advantage to dropping the raft down by 3.3 m (10.8 ft), was it allowed for creation of a large 725-m³ (25,603-cf) rainwater storage tank inside the core. The tank further contributes to the project’s pursuit of Gold certification under the U.S. Green Building Council’s (USGBC’s) Leadership in Energy and Environmental Design (LEED) program. This is because it enables the harvesting of rainwater for use within the building.
The upper portion of the core void was used for an air passage to connect the two earth tubes together before entering the central air handler. As a final multifunctional use of a concrete structure, the storm flows for the site are piped to, and stored in, a 400-m³ (14,125-cf) surface tank that also provides footing walls for the complex multi-level west entrance plaza.
Curtain wall
The building envelope plays a critical role in energy use, particularly in an extreme climate. The envelope is vital to maintain adequate occupant comfort and provide a thermal barrier to the outdoors. It also helps minimize the effect of large temperature swings.
The EPCOR Tower building envelope has a window-to-wall ratio (WWR) of 49 per cent that uses an Ontario-made unitized curtain wall system, with panels craned into place after being delivered to the site. A ‘stick-frame’ system was utilized in the balcony areas to accommodate the differential movement experienced by the curtain wall and structural systems.
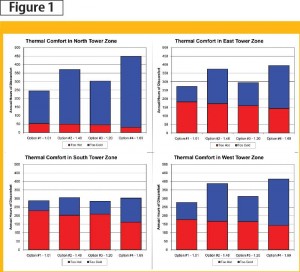
Image courtesy Integrated Design
To ensure optimal building envelope performance was achieved, four curtain wall options were evaluated for both energy cost and thermal comfort. A full building energy model that used EE4 Version 1.71 was used to compare the annual energy costs of these four options (Figure 1). The software provided thermal comfort results based on defined temperature ranges.
The U-value of the overall glazing system selected was calculated to be 1.23 W/m2K (0.216 Btuh/sf-F). A computational fluid dynamics (CFD) simulation (Figure 2) was used to determine perimeter heating could be eliminated by modelling a full typical office bay to calculate the interior temperatures. The simulation model determined the temperature at the inside pane of glass on a winter design day to be 15.1 C (59.2 F).
Elevators
EPCOR Tower incorporates 16 elevators in total. There is a trio of machine-roomless (MRL) parkade shuttle elevators that travel at 106 m (350 ft) per minute. These three elevators are located at the east end of the building and provide service to all four underground parkade levels and to the main and second floors.
Six heavy-duty gearless traction low-rise elevators are positioned in two facing banks of three elevators and travel at 213 m (700 ft) per minute, providing service between the main and second floors, and office floors three through 14, with a capacity of 1814 kg (4000 lb).
Additionally, another six heavy-duty gearless traction high-rise elevators are positioned in two facing banks of three elevators. They travel at 365 m (1200 ft) per minute, providing service between the main and second floors, and office floors 14 through 28 with a capacity of 1588 kg (3500 lb).
Further, there is a heavy-duty gearless traction service elevator with an oversize cab that travels at 152 m (500 ft) per minute. This provides service from the inside loading dock at the P1 parkade level to all occupied floors (main through 28), as well as the mechanical penthouse on the 29th floor, with a capacity of 2268 kg (5000 lb).