The hidden hero: Why air barriers matter more than ever
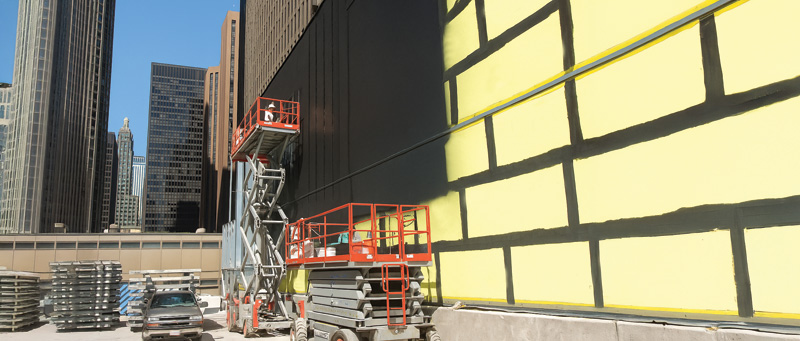
Today’s construction industry faces a growing list of expectations. Building enclosures must be more than just weather-tight; they are expected to be energy-efficient, moisture-resilient, durable, and comfortable across a wide range of seasonal extremes. This challenge is even greater in Canada, where buildings must endure freezing winters, humid summers, and frequent freeze-thaw cycles.
To meet these demands, architects and builders must understand the “four control layers” that govern building enclosure performance: thermal, vapour, air, and moisture. While each layer is essential, the air barrier often plays a disproportionately important role; yet it remains one of the most misunderstood components in enclosure design.
This article explores air barriers’ vital role in Canadian construction, how they interact with other systems, and why innovations like spray-applied polyurea are changing the game for commercial enclosures.
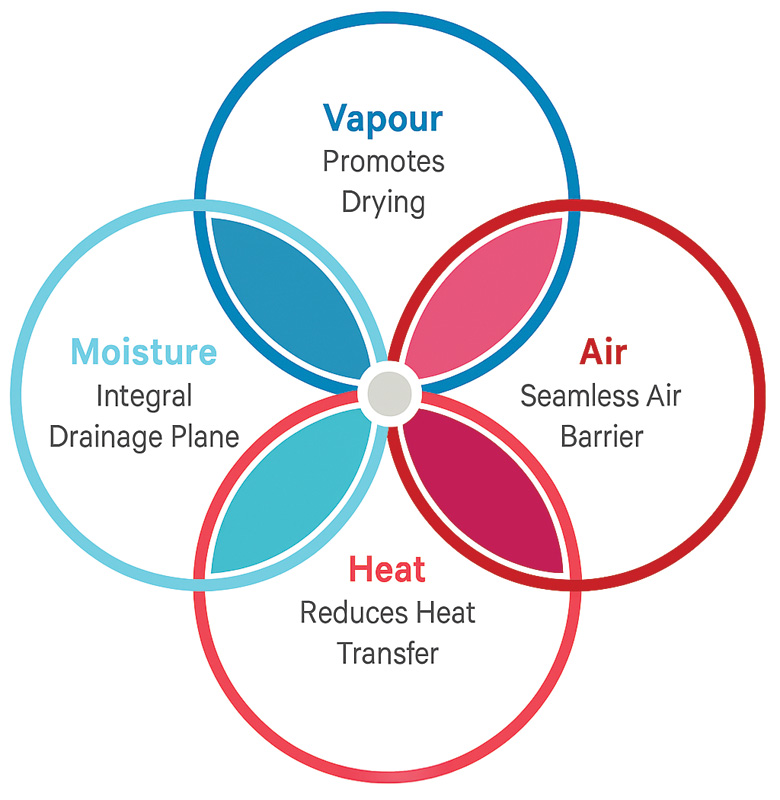
What is an air barrier and why does it matter?
An air barrier is a system of interconnected materials that controls the unintended flow of air in and out of a building. Its primary role is to restrict air leakage through gaps, joints, penetrations, and porous materials—not to be confused with insulation, which slows heat transfer. By stopping air movement, an air barrier reduces the transport of heat, moisture vapour, and pollutants.
Air leakage is more than a nuisance—it significantly impacts energy efficiency, durability, and indoor air quality (IAQ). According to Natural Resources Canada (NRCan), uncontrolled air leakage can account for up to 40 per cent of a building’s total energy loss. That translates to wasted energy, higher costs, increased emissions, and reduced occupant comfort.
Beyond energy performance, uncontrolled airflow moves moisture-laden air into building assemblies, where it can condense and cause mould, rot, and material degradation. This is especially problematic in Canadian climates, where large indoor-outdoor temperature differences drive strong pressure differentials, pushing moist indoor air into cold wall cavities. To be effective, an air barrier must be:
- Continuous, with no gaps or unsealed joints across the building enclosure
- Durable, able to withstand jobsite handling and the thermal and structural movement that occurs over the life of the building
- Compatible with adjacent components, including insulation, vapour retarders, and flashing materials
Ultimately, the air barrier is a critical piece of the building performance puzzle, essential for meeting building codes, improving occupant comfort, and delivering long-term value in residential and commercial construction.
Where air barriers belong
In commercial construction, the most effective location for an air barrier is typically on the exterior side of the structural wall. Applied to substrates such as exterior gypsum board, oriented strand board (OSB), or concrete, this placement provides a continuous, uninterrupted surface, essential for airtightness across the enclosure.
Exterior installation offers key advantages. It minimizes interruptions, simplifying detailing around penetrations and transitions. It also allows the barrier to be supported by the wall structure, helping it resist wind loads, pressure differentials, and building movement. Additionally, placing the air barrier externally simplifies integration with insulation and flashing, ensuring continuity across complex assemblies.
While interior air barriers are still used in some residential or retrofit situations, they can be harder to detail around partitions, services, and framing. Exterior air barriers, especially when paired with continuous exterior insulation, offer superior durability, moisture control, and long-term energy performance, making them the preferred choice for modern commercial projects targeting stringent energy codes and sustainability goals.
Types of air barriers in Canadian construction
Canada’s diverse climate zones, from the damp coastal regions to the frigid North, demand high-performing and versatile air barrier systems. Builders have several air barrier options, and the right choice depends on the project’s complexity, location, budget, and construction sequence. Each type brings unique advantages and installation considerations.
Self-adhering sheet membranes
Self-adhered sheet membranes are one of the most commonly used air barrier systems in commercial construction. These rubberized asphalt sheets with polymeric facers are supplied in rolls and applied to primed substrates such as gypsum, concrete, or plywood.
Advantages:
- Strong adhesion to smooth, primed surfaces
- Good resistance to air and moisture infiltration
- Reliable sealing around fasteners, joints, and detailing transitions
- Many products offer limited vapour permeability, depending on formulation
However, success with sheet membranes depends heavily on proper surface preparation and precise installation. Misalignment or wrinkles can compromise performance, and detailing corners or irregular shapes requires skill and additional components. These membranes are best suited to flat, uniform surfaces and projects where sequencing allows meticulous application.
Closed-cell spray polyurethane foam (ccSPF)
Closed-cell sprayfoam is unique because it acts as a four-in-one control layer, providing thermal insulation, air sealing, vapour resistance, and moisture control in a single product. Applied directly into wall cavities or over exterior sheathing, ccSPF is popular in commercial and residential construction, particularly for complex geometries and tight spaces.
Advantages:
- High R-value per inch (approximately R-6 per inch, RSI 1.06), minimizing wall thickness
- Superior adhesion to various substrates, including wood, concrete, and steel
- Conforms easily to irregular or curved surfaces
- Minimizes thermal bridging, especially when applied as continuous insulation (c.i.)
Despite its benefits, ccSPF does come with considerations. It must be shielded from UV light, often requiring protective cladding or coatings. In commercial applications, it also needs to be co-ordinated with thermal barriers for fire protection compliance. Additionally, installation must be performed by certified applicators, as improper ratios or ambient conditions can affect performance.
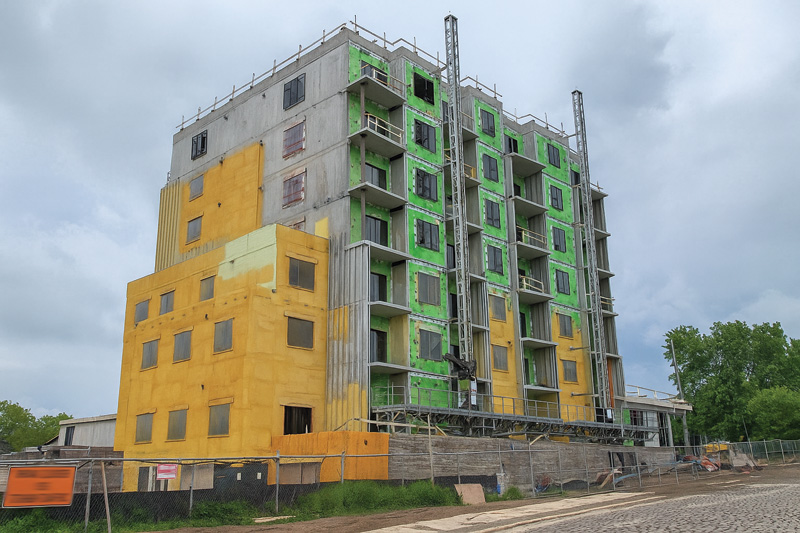
Liquid-applied and spray-applied membranes
Liquid and spray-applied air barriers have grown rapidly in popularity, especially in high-performance and net-zero energy buildings. These materials, ranging from water-based acrylics to polyurethanes and elastomers, are applied by roller, brush, or spray equipment, forming a monolithic membrane directly on the substrate.
Advantages:
- Seamless application, eliminating the need for taped joints or overlaps
- Excellent flexibility, accommodating structural movement and cracks
- Superior detailing capabilities around penetrations and transitions
- Effective over irregular or non-uniform surfaces, including concrete masonry unit (CMU) and corrugated sheathing
Liquid membranes reduce the complexity of traditional assemblies, making them a good choice for retrofits, mass timber buildings, and complex facade geometries. Some products are vapour-permeable, supporting drying strategies in wall assemblies, while others provide full vapour resistance, giving designers a wide range of performance options.
By understanding each system’s strengths, limitations, and application methods, project teams can optimize building envelope performance and ensure the air barrier integrates effectively with other control layers. Whether prioritizing durability, drying potential, ease of installation, or long-term energy efficiency, Canadian builders have a robust toolkit tailored to the demands of modern, climate-responsive construction.
Why air barriers must survive the real world
Air barrier systems are critical to long-term building performance, but only if they can withstand time. In theory, most air barrier materials perform well in laboratory conditions, where application is controlled and consistent. However, the real-world construction environment is far less forgiving. Jobsite conditions, installation sequencing, mechanical damage, and weather exposure all present challenges that can compromise the integrity of the air barrier, sometimes before the building is even enclosed.
In Canada, where buildings are routinely exposed to extreme temperature swings, high winds, and prolonged freeze-thaw cycles, the durability of air barrier systems is more than just a nice-to-have; it is essential. A compromised air barrier reduces energy efficiency and allows bulk water, moisture vapour, and contaminants to penetrate the building enclosure, leading to structural degradation, IAQ issues, and higher maintenance costs.
Construction site realities
The construction site is a dynamic environment with multiple trades working simultaneously under tight timelines. Windows and doors may not be installed when the air barrier is applied. Trades may fasten materials to walls, cut penetrations for mechanical systems, or adjust layouts, activities that can damage or disrupt air barrier continuity. Even storing materials or placing scaffolding against a wall can tear, puncture, or peel air barrier components.
This is especially problematic with rigid or thin membranes prone to mechanical damage. Sheet membranes may peel or tear at corners and transitions. Liquid-applied systems, if too thin or not fully cured, can be compromised by rain, dust, or impact. Sprayfoams may be gouged during framing or cladding work.
To remain effective, an air barrier system must be robust, not only when complete but also throughout construction staging and sequencing. That means:
- Adhering well to a variety of substrates, even in less-than-ideal surface conditions
- Tolerating incidental exposure to UV, moisture, or freeze-thaw before being covered
- Withstanding mechanical damage from scaffolding, trades, and weather
- Remaining flexible enough to accommodate minor movement or substrate shrinkage
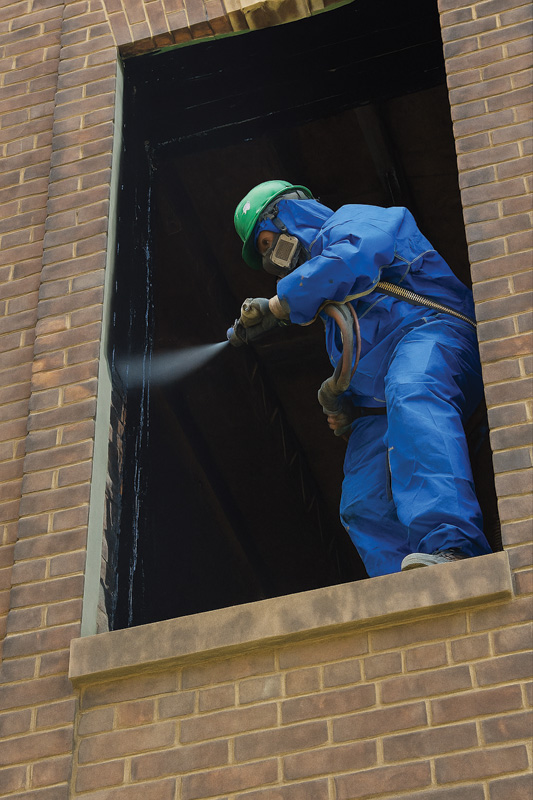
Durability is a system attribute
Durability is not the property of a single material; it is a system-level trait. Every air barrier assembly includes transitions, fasteners, primers, sealants, and flashing. Even if the primary membrane performs well, failure can occur at joints, terminations, or substrate changes if components are incompatible or poorly adhered. This is why manufacturers often offer tested system packages that ensure long-term compatibility and performance.
Materials such as polyurea air barriers are engineered to meet these challenges. Polyurea provides high elongation (more than 300 per cent), enabling it to stretch with structural movement without tearing. Its tough, rubber-like finish resists punctures and abrasions during construction. With rapid cure times and weather resistance during application, polyurea often outperforms traditional systems in harsh or fast-track projects.
However, polyurea’s performance relies on specialized equipment and trained installers. Like any air barrier, even the most durable materials can fail if not installed correctly.
Installation quality: The human factor
Durability is not just a property of materials; it reflects the installation process. A well-installed, moderately durable air barrier will outperform a premium product poorly applied. Temperature, humidity, substrate moisture, surface preparation, and film thickness affect performance. This is why many builders now use third-party inspections and quality assurance programs, such as those from the Air Barrier Association of America (ABAA) and supported by Canadian codes. Blower door tests, adhesion pull-tests, and site mock-ups are increasingly common in commercial construction, helping ensure that what is designed on paper is built in the field. Air barriers are only as good as their weakest link. For the system to perform over the building’s life, it must:
- Be resilient enough to survive the rigours during construction
- Be designed as a complete system, not just a standalone product
- Be installed with skill, oversight, and attention to detail
With tightening energy codes and growing demand for high-performance enclosures, durability is no longer optional; it is central to success. Selecting the right system and installing it correctly means fewer callbacks, lower lifecycle costs, and buildings that perform as intended, today and decades from now.
The crucial role of air barriers in wall assemblies
Controlling moisture is one of building science’s most critical and complex challenges. While rain and plumbing leaks are often at the top of mind, much of the moisture that affects wall assemblies comes from air leakage and vapour diffusion. Air barriers play a central role in mitigating these risks and ensuring long-term durability, particularly in Canada’s diverse and often extreme climate zones.
Air barriers influence moisture behaviour in three key ways:
Air leakage—driven vapour transport
This is the primary mechanism of moisture movement in most buildings. When warm, humid air leaks through cracks and gaps in the building envelope, it carries water vapour. If this air reaches a cooler surface, such as the backside of sheathing or an insulated cavity, it can condense, leading to rot, mould, and corrosion. A continuous, airtight barrier is the most effective way to stop this movement at its source.
Bulk water resistance
The air barrier often doubles as a secondary weather barrier in exposed wall assemblies, especially those without an exterior rainscreen. When properly detailed with sealed transitions and flashing, air barrier membranes can resist wind-driven rain and bulk water infiltration, providing an added line of defence behind the cladding.
Vapour diffusion control
The vapour permeability of the air barrier material can also influence the wall’s drying potential. Vapour-permeable air barriers allow water vapour to pass, while impermeable ones limit drying, so their placement and compatibility with other materials must be carefully considered.
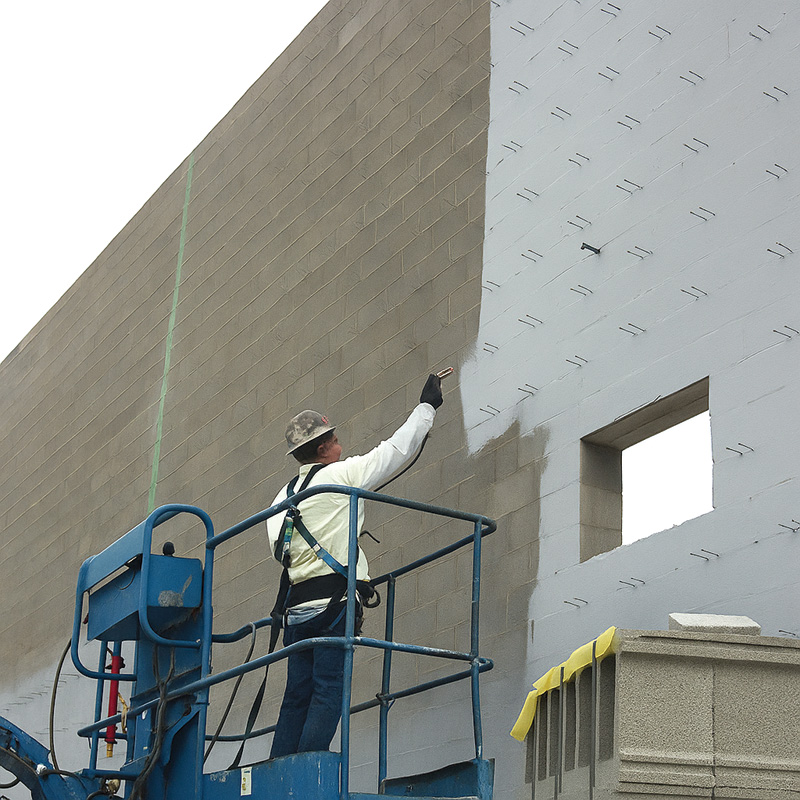
Insulation strategies and dew point control
Moisture risk is closely tied to temperature gradients within a wall. As warm indoor air moves outward in winter (or inward in summer), it cools, and condensation occurs if it reaches the dew point temperature. This is why the location and ratio of insulation play such a significant role in managing condensation risk.
- All-interior (inboard) insulation: Historically, walls with all-interior insulation often used a vapour-impermeable (vapour-closed) air barrier on the exterior and a vapour retarder on the inside, limiting the wall’s ability to dry. For future projects, using an inboard insulation with a vapour retarder or impermeable insulation, the air barrier should ideally be vapour-permeable. This allows outward drying if moisture enters the wall cavity.
The interior insulation must be carefully specified if a non-permeable exterior air barrier is preferred. In this case, the insulation should be vapour-permeable, and a smart vapour retarder should be installed on the warm side to enable drying toward the interior.
- All-exterior (outboard) insulation: All-outboard insulated wall enclosures differ from all-inboard insulated walls in two ways. First, the vapour barrier is located on the warm side of the assembly. In typical outboard-insulated assemblies, this places the air and vapour control layers inboard of the dew point, which tends to fall within the continuous insulation. As a result, the risk of condensation at the vapour barrier is reduced, and dew point calculations may not be necessary in many cases. However, careful moisture analysis is still recommended to confirm performance under specific project conditions. Building science is objective, but typical recommendations for air barrier permeance in exterior insulated walls are as follows: with permeable exterior insulation (mineral wool), either a vapour-permeable or vapour-impermeable air barrier may be used; with impermeable insulation
(e.g. SPF, XPS), a vapour-impermeable air barrier is recommended. These are general guidelines, and an enclosure study is always ideal once all components are selected. - Split-insulated assemblies: Split-insulated systems differ from the other two systems because the dew point shifts between the interior and exterior insulation with seasonal temperature changes. As a result, the air barrier’s vapour characteristics must be selected and validated, ideally through hygrothermal analysis, to prevent interstitial condensation. If advanced software is not available, a rule of thumb is: when the interior insulation is ccSPF or permeable insulation with a vapour retarder, pair it with a vapour impermeable air barrier and exterior open-cell sprayfoam insulation (ocSPF) and/or mineral wool to allow drying to the exterior. If using a vapour-impermeable air barrier with a permeable insulation, the interior side should feature permeable insulation with a smart vapour retarder to facilitate drying inward. As always, a full enclosure review is recommended before finalizing the design.
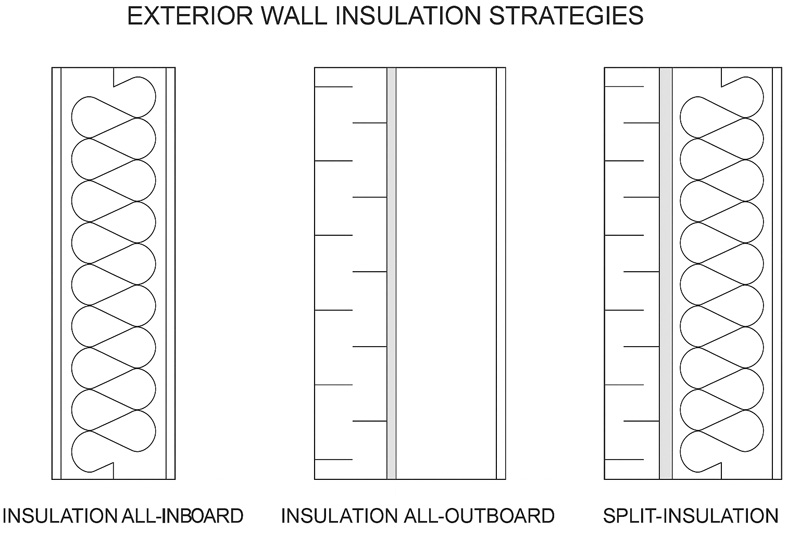
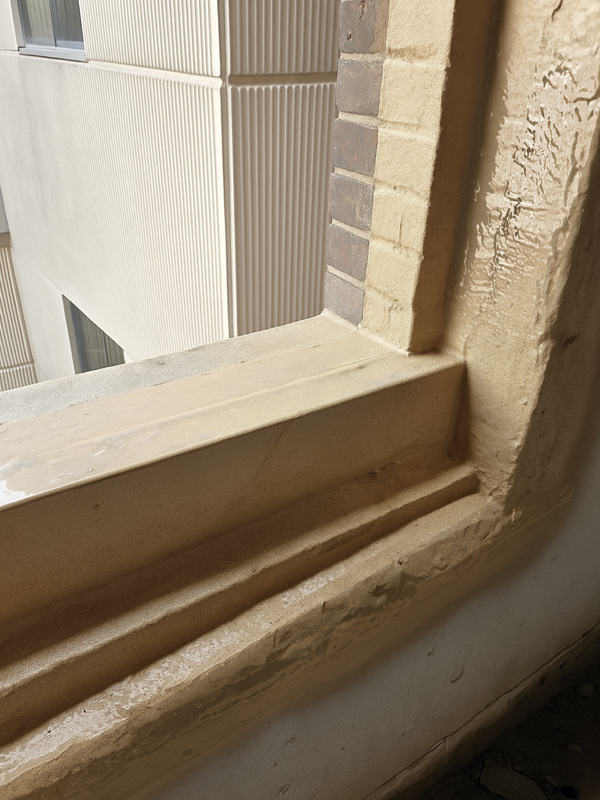
Designing for drying: Best practices in modern construction
Moisture control today is not just about stopping water from getting in, but also about ensuring it can get out. Many older buildings used vapour-closed materials on both sides of the wall, unintentionally trapping moisture within. Modern best practices prioritize one- or two-directional drying, enabling assemblies to release moisture safely to the interior or exterior.
This can be achieved by:
- Selecting vapour-permeable air barriers on the exterior when the interior has a low-permeability vapour retarder
- Using smart membranes that adapt their permeability based on relative humidity (RH), offering more drying potential when moisture levels are high
- Avoiding impermeable materials on the exterior, which have the potential to trap moisture in the assembly
Hygrothermal modelling software such as WUFI is increasingly used for complex projects or buildings to simulate real-world moisture behaviour. These tools help designers understand the long-term impact of temperature, humidity, vapour drives, and solar loading, ensuring assemblies are energy efficient and durable.
Polyurea air barrier technology
One of the most exciting advancements in air barrier technology is the use of spray-applied polyurea. Known for its use in industrial coatings, polyurea is now being adapted for building enclosures thanks to its unique properties:
Key benefits
- Fast-curing: Tack-free in under 30 seconds and supports high production rates
- Cold-weather application: Can be applied in sub-zero temperatures, ideal for Canadian winters
- High elongation: More than 300 per cent flexibility, accommodating building movement
- Seamless membrane: No seams, no fasteners, no tape, just one monolithic layer
This makes polyurea a particularly good fit for:
- Mid-to high-rise commercial and institutional buildings
- Complex geometries or irregular substrates
- Projects with short construction schedules or winter timelines
Conclusion
In Canadian construction, the air barrier is not just a product but a system and strategy. It is vital in high-performance enclosures, contributing to energy efficiency, moisture control, and long-term durability. Whether using traditional membranes or advanced polyurea coatings, success depends on understanding how the air, vapour, thermal, and moisture layers work together. By limiting air movement, air barriers improve comfort and help prevent condensation, mould, and structural damage.
Air barriers have evolved, with innovations such as spray-applied polyurea offering faster installation and greater durability, which is especially useful in Canada’s demanding climate. These solutions respond to challenges such as labour shortages and the need for speed and reliability. Still, proper installation is critical; even high-performance materials can fail if poorly applied.
Understanding how air barriers interact with vapour and insulation layers is essential to building durable, resilient enclosures. A well-integrated, robust air barrier system is essential for high-performance buildings to succeed over time. As the industry advances, adopting innovative materials and techniques will be key to building energy-efficient, long-lasting structures. Smart wall design goes beyond sealing; it enables buildings to dry, perform, and endure Canada’s harsh climate.
Authors
Rockford Boyer, B. Arch. Sc., MBSc, BSS, is an experienced building science leader at Elastochem with more than 20 years of expertise in sustainable building design. He holds an undergraduate degree in civil engineering and architecture and a master’s in building science. He is also a member of Passive House Canada and the Ontario Building Envelope Council (OBEC). He is also a part-time professor at Sheridan College, teaching in the architectural technology program and sharing his knowledge and expertise with future generations of architects and designers.
As the vice-president of marketing at Elastochem, Betsy Cosper uses her extensive global expertise in building materials commercialization and sustainability strategy. She has gained international leadership experience across the construction, horticulture, and advanced materials sectors, holding a BSc honours and an MBA.