NBC 2020 defines key fire barriers at edge-of-slab joints
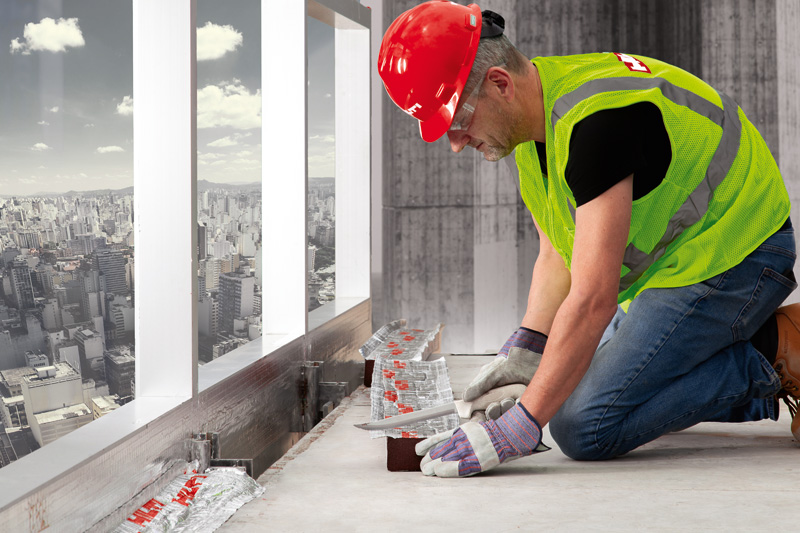
Curtain walls, by definition, are exterior walls that “hang” away from the building floor slabs rather than sitting on top of the floor as a window wall would. This inevitably creates a gap between the outside edge of the floor slab and the inner surface of the curtain wall.
In a multi-storey building, any gap in a floor that could allow a path for fire and/or smoke to spread between stories is a significant hazard. Such a spread could result in a fire being established in two or more storeys in a short period before the deployment of fire department personnel and fire-fighting resources to the building’s interior. A multi-storey fire could easily result in an out-of-control situation, causing a significant hazard to building occupants and the responding fire personnel.
To prevent fire spread between stories in buildings tall enough or large enough to require fire-resistance-rated floors, the National Building Code of Canada (NBC) has long had requirements to close all gaps in a fire-resistance-rated floor with materials and systems that would provide “continuity” of the fire resistance of the floor slab. The concept of “continuity” is important enough to appear more than 80 times in the code.
Before examining the latest code requirements, it is useful to step back to see what the edge-of-slab joint fire protection requirements were in previous code editions. Article 3.1.8.3 of NBC 2015 stated the requirement as follows:
3.1.8.3 Continuity of Fire Separations
4) The continuity of a fire separation shall be maintained where it abuts another fire separation, a ceiling, a roof, or an exterior wall assembly.
(See Note A-3.1.8.3.(4).) A-3.1.8.3.(4) Fire Separation Continuity. The continuity of a fire separation where it abuts against another fire separation, a floor, a ceiling, or an exterior wall assembly is maintained by filling all openings at the juncture of the assemblies with a material that will ensure the integrity of the fire separation at that location.
The building code has traditionally taken a performance-based approach, outlining the requirement for floor slab continuity at the intersection of an exterior wall but without specifying deemed-to-comply solutions. Previously, the code did not provide clear guidance on how designers or contractors should achieve fire resistance at the edge-of-slab gap. In contrast, the updated code introduces precise and practical requirements, offering much-needed clarity.
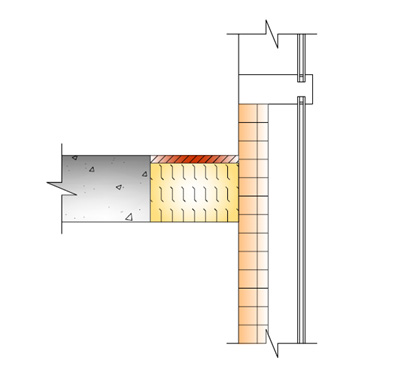
Many knowledgeable Canadian design and construction professionals have been specifying and installing perimeter joint firestopping systems tested and listed for this purpose (discussed further) to comply with this requirement. However, the 2015 NBC can be interpreted to mean it would be acceptable to simply extend the fire rating of the floor slab out to the curtain wall across the edge-of-slab gap, using some approved materials within the gap of unquantified performance, and not considering the construction and fire behaviour of the curtain wall itself. This would provide “continuity” of the rating of the floor slab. Therefore, something similar to what is shown in Figure 1 might have been approved in some cases.
Over the past 20-plus years, fire testing has shown that trying to prevent storey-to-storey vertical fire spread by focusing only on the gap at the edge-of-slab would not provide sufficient protection. Typical curtain wall components will bend, expand, melt, and/or break when exposed to the intense heat of a fire in the storey below. To give a trivial example, if a spandrel panel exposed to fire bends and expands/flexes outwards, this could open a gap, even if the gap were filled and sealed pre-fire with mineral wool and a firestop sealant.
Based on fire test results, the clear takeaway has been that all the curtain wall components need to be considered when establishing the correct firestop design solution. The 2020 NBC did what other codes around the world have already done, which is to specify the specific fire test method that must be used to evaluate and quantify the adequacy of the perimeter joint firestopping, using a fire test protocol that incorporates the effect of the curtain wall construction details. The chosen fire test method was ASTM E2307, Standard Test Method for Determining Fire Resistance of Perimeter Fire Barriers Using Intermediate-Scale, Multi-story Test Apparatus. This same test method is referenced in codes in many other countries, including the United States and the IBC. The NBC 2020 code requirement reads as follows:
3.1.8.3. Continuity of Fire Separations
4) Except as provided in Sentence (5), joints located in a horizontal plane between a floor and an exterior wall shall be sealed by a firestop that, when subjected to the fire test method in ASTM E2307, “Standard Test Method for Determining Fire Resistance of Perimeter Fire Barriers Using Intermediate-Scale, Multi-story Test Apparatus,” has an F rating not less than the fire-resistance rating of the horizontal fire separation.
The required fire-resistance rating (F rating) of the perimeter joint system must be equal to the fire-resistance rating of the floor slab. If the building is small enough and/or short enough, as defined by the building code, that the code does not require any rating for the floor slab, then perimeter joint firestopping is not required.
ASTM E2307 is referenced within the Canadian test method CAN/ULC-S115 for testing perimeter joint fire stopping without any modifications. Future editions of the NBC will likely be revised to reference CAN/ULC-S115 for the perimeter joint firestop requirement instead of E2307. Practically speaking, that would not be a technical change. The required fire test method would be unchanged. It would be referenced differently, indirectly via CAN/ULC-S115.
ASTM E2307 fire test and listings
ASTM E2307 took approximately 10 years to develop and issue as a published standard. The long development time was due to a years-long debate regarding what the pass-fail criteria of the test method should be.
It was acknowledged that curtain walls are built such that they are not fire-resistance-rated assemblies, nor are they required to be fire-resistance-rated per the building code. They are generally not designed or intended to stop fire from moving from inside the building to the outside, nor are they designed to prevent a fire lapping the outside from re-entering the building at some storey above.
All other fire resistance tests dealing with the intersection (joint) between two assemblies always involve both intersecting assemblies being fire resistance rated. When subjected to a fire test, it was not obvious what performance should reasonably be expected of a non-fire-rated assembly (the curtain wall).
The ASTM fire test standards committee finally agreed that the curtain wall itself did not have to be fire-resistance rated per se. That would be an unjustified requirement, given that building codes do not require it. However, how that curtain wall behaves and reacts under fire exposure is a key variable that must be accounted for in establishing the correct assembly of materials to prevent interior fire spread at an edge-of-slab gap.
The pass/fail criterion was thus accepted to be flame penetration only at the perimeter joint protection or its boundaries or the passage of flames or hot gases through the joint protection sufficient to ignite a cotton pad. ASTM E2307 does not mandate any specific behaviour or temperature rise limitation of the curtain wall components. However, as mentioned, the curtain wall details will determine whether any proposed seal of the edge-of-slab gap will prevent vertical fire spread. When exposed to the fire test, the behaviour of the curtain wall framing, spandrel, and other wall components will determine whether a proposed seal of the perimeter gap will achieve the desired fire resistance rating.
The deflections, movement and/or melting of various curtain wall components during fire exposure will be a strong determining factor in whether the materials used to seal the edge-of-slab gap, and the installation methods for those materials, will succeed or not to prevent fire spread from the storey below to the storey above via the edge-of-slab joint.
The E2307 fire test assembly is a two-storey apparatus with a fire exposure room on the lower storey and an observation room on the upper storey. A unique feature of the ASTM E2307 fire test is it exposes the curtain wall spandrel to fire exposure from two sides: from the inside below the floor slab and the outside above the window of the lower floor. This is meant to simulate the highly possible condition of a fire on the lower floor, breaking the windows and emerging out of the building.
ASTM E2307 has now been in use for 20 years. Due to its reference in the building codes of many countries and for many years (since 2006 in the IBC), many tested and listed perimeter joint firestop systems are available. As of this publication date, UL Solutions has 232 tested and listed systems using this standard, and Intertek has 314 systems. These are the eight main variables that each of those systems specify in detail to make clear to what specific curtain wall details a given system listing would apply:
- Framing (e.g. steel or aluminum)
- Spandrel material (e.g. concrete, glass, stone)
- Spandrel insulation—type, density, thickness, attachment method
- Dimensions of spandrel panel (if any), height of spandrel panel above floor line
- Insulation covers (if) needed over transoms or mullions
- Size of the edge-of-slab gap
- Firestopping part 1—type, density, and compression of safing insulation (insulation in edge-of-slab gap)
- Firestopping part 2—type, thickness, and overlap of sealant needed over the safing insulation
Items six and seven are sometimes combined when a preformed firestop solution is used.
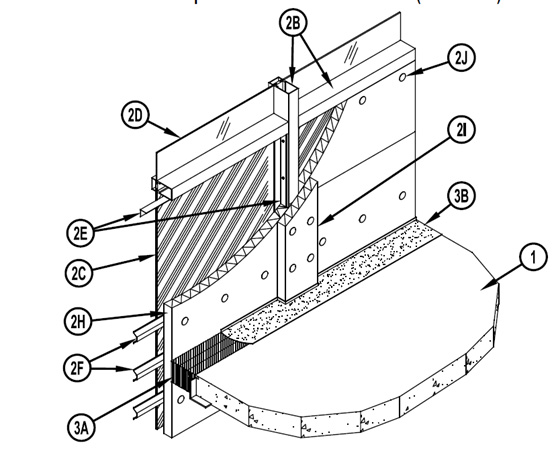
Additional curtain wall components beyond the eight mentioned are often specified in the listings if determined by the listing laboratory to be important to the fire performance of the perimeter gap protection. Figure 2 shows an example of a curtain wall firestop system. The large number of details shown in the listing, which the listing laboratory deemed critical, is typical. Such a comprehensive enumeration of the wall and joint details in the listing resulting from an ASTM E2307 fire test will help ensure the designer or contractor will select a suitable match for the wall being built and thus ensure the fire resistance rating indicated in the listing will be achieved.
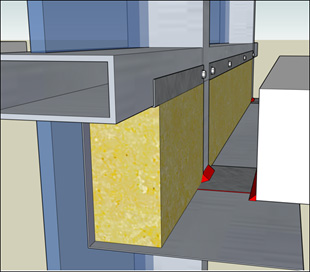
Curtain wall assemblies that have a floor-to-ceiling glass with a small spandrel extending below the floor line, or curtain walls with all vision glass (often referred to as “zero spandrel” curtain walls), must be constructed and protected in particular ways to prevent fire spread between stories. A perimeter joint firestop system listed with a wall having spandrel panels would not apply to zero spandrel wall assemblies and vice versa. Zero-spandrel curtain wall firestop systems often rely on insulated steel shadow boxes to help create the firestop system which would prevent vertical fire spread. Figure 3 shows a simplified example of a shadow box installed in a zero-spandrel curtain wall, thus providing the foundation for possible firestopping of the remaining safing gap. The shadow box is filled with stone wool (mineral wool) 120 kg/m3 (nominal 8 lb/ft3) density, with layers (fibre axis) to be vertical.
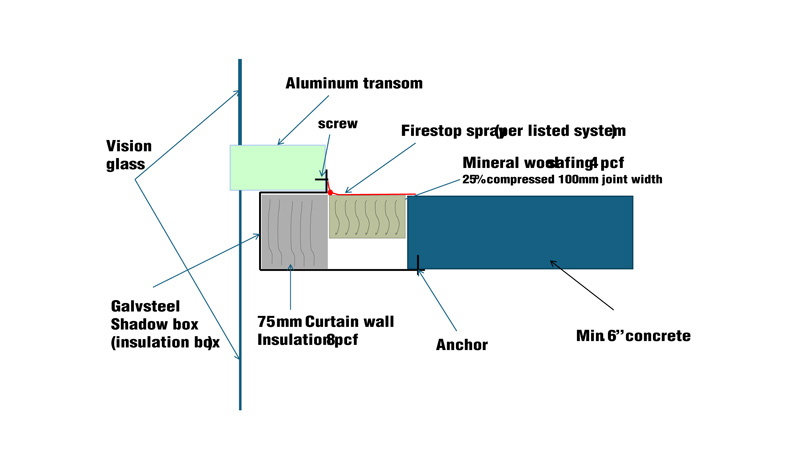
Figure 4 shows an example of a listed firestop system for a zero-spandrel curtain wall.
Important tip: Verify a proposed system listing, or the system listings referenced within a proposed Engineering Judgment (EJ), are sufficiently similar in all important variables to the needed wall installation.
The most critical items that must match between a proposed field installation and the tested/listed firestop system are:
- a) the spandrel type
- b) framing type
- c) spandrel insulation
If other details do not match, an EJ can often be obtained from a firestop manufacturer with E2307 fire test data. However, any offered EJ should reference tested systems that at least match items a, b, and c.
Important tip: Perimeter joint firestop system listings for curtain walls using spandrel panels will not provide a suitable basis for an EJ if the target wall is zero-spandrel or floor-to-ceiling glass.
A firestop manufacturer may be willing to offer an EJ based on one of their tested systems to accommodate some differently constructed curtain walls. The issuance of an EJ does not guarantee that the proposed solution will provide the required fire-resistance rating. Similar to proposed installation details from any vendor, an EJ is a recommendation from the issuer, who has a vested interest in its acceptance and implementation. It is ultimately the responsibility of the recipient to critically assess the EJ’s validity.
Manufacturers, naturally motivated to offer solutions to potential customers, may propose options they believe are “close enough,” even when a thorough evaluation might reveal that the conditions do not sufficiently align with tested assemblies. To ensure compliance and effectiveness, recipients should carefully scrutinize proposed EJs, verifying that key parameters align with relevant fire test data.
To help the recipient of a proposed EJ assess whether the EJ should be accepted/approved or not, the International Firestop Council (IFC) has published a document entitled “Recommended IFC Guidelines for Evaluating Firestop Engineering Judgments – Perimeter Fire Barrier Systems.”1 An EJ meeting the IFC Guidelines would explicitly list the tested and listed systems being referenced in supporting the conditions of the EJ. The receiver and/or approver of the EJ should verify the referenced listings have details that are reasonably similar to the offered EJ. If not, the issuer of the EJ should be asked to justify on what basis the referenced listings were extrapolated to meet the conditions of the present field condition. Evaluating an EJ, as the IFC Guidelines suggest, is subjective. With the IFC guidance, most people can detect when they are being offered an EJ that does not have a sufficient basis in past testing. An EJ that is too far removed from the presently needed conditions should not be accepted or approved. Inadequate perimeter joint firestopping installed throughout a building, one storey after another, creates a possible danger to occupants and potential liability that should be avoided.
The one approving (or not) a submitted EJ will depend on the job, and could be the design professional in responsible charge, the installation contractor, or some Authority Having Jurisdiction (AHJ) if there is strong and knowledgeable local code enforcement.
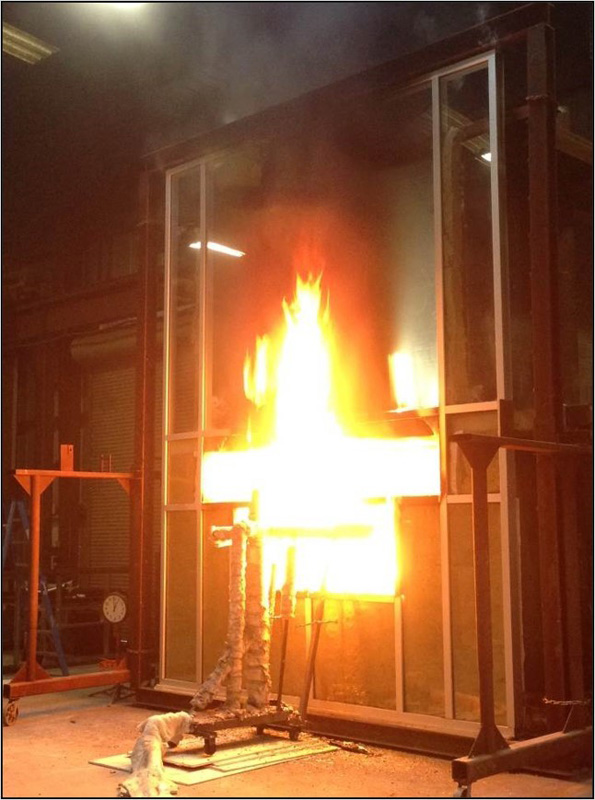
To help encourage a higher degree of reliability and technical soundness of issued firestop EJs, in 2024 UL Solutions launched the “Technical Evaluation Developer Program” (TEDP). UL Solutions uses the term “technical evaluation” as their alternative term for EJ in this program. It is a voluntary program for firestop manufacturers. UL examines the knowledge level of the technical staff developing EJs and evaluates the quality and consistency of the internal process for developing EJs. UL conducts audits to assess a manufacturer’s management system (MS), ensure adherence to the MS, and evaluate the MS regarding the program’s requirements. UL will select a sampling of the EJs issued within a given year for fire testing to verify if the EJs predict the fire-resistance rating the previously untested engineered designs can achieve sufficiently closely. Those manufacturers’ offices meeting the program requirements are accredited and listed by UL within their Category Control Number (CCN) “WYGB.” Accredited companies can be found at ul.com/piq by searching for CCN (listing category) WYGB. It might seem that a curtain wall designer needs to browse the 500-plus available perimeter joint firestop listings to find a suitable firestop for any wall design. In fact, in many cases, the proposed curtain wall design details may need to be modified to some extent to make the firestopping possible, either in accordance with a tested/listed system or with a well-justified EJ. As any firestop manufacturer with this kind of fire test experience can say, there are curtain wall conditions that would not pass an E2307 test and, therefore, could not be feasibly provided with an EJ. If no wall design changes are made, a conscientious firestop manufacturer asking for an EJ may offer a design that indicates something labelled as “smoke seal only” without indicating any anticipated F-rating. This expresses honestly that they cannot reasonably assure a quantifiable fire resistance rating equal to the rating of the floor slab.
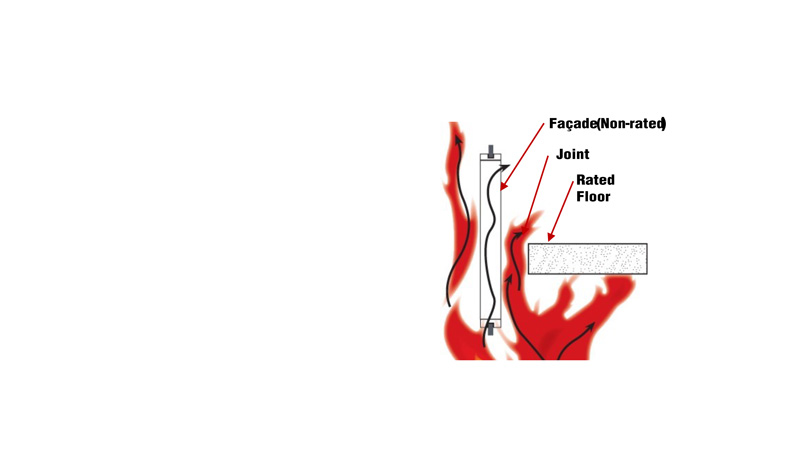
In the past, when NBC 2015 and previous editions required only the “continuity” of the floor fire resistance, EJs were offered and often approved even if the manufacturer offering the EJ did not have any relevant fire test data on the behaviour of the target wall type. Many EJ issuers included caveats/disclaimers similar to these:
- “Curtain wall design by others”
- “Rating of this system is dependent on the performance of surrounding construction”
- “Rating up to X hours, or as long as the assembly remains intact in a fire scenario”
These disclaimers made it plain that the company offering the EJ did not know how the curtain wall construction might affect its proposed firestopping of the perimeter joint.
Seeing such a disclaimer should be considered a red flag now that NBC 2020 mandates a perimeter joint firestop tested to ASTM E2307. E2307 is not simply a joint test. It is a test of a complete curtain wall assembly. The construction details of the curtain wall are a larger factor in determining the fire resistance rating of the perimeter joint firestopping than the materials in the safing gap.
Important tip: A proposed perimeter joint firestop EJ with a disclaimer indicating that precise curtain wall construction details have not been considered is unlikely to meet the intent of NBC 2020.
To offer system listings or justified EJs compliant with NBC 2020 for many jobs, firestop manufacturers should (if they have not already) invest in and accumulate sufficient E2307 fire test data. Such fire testing will, first and foremost, result in listed designs. Just as importantly, comprehensive E2307 fire test experience can provide relevant fire test data to justify some EJs. The variety of curtain wall variations for which a firestop manufacturer could offer well-supported EJs will be proportional to the extent of their E2307 fire test experience. Some have a large body of listings and some do not.
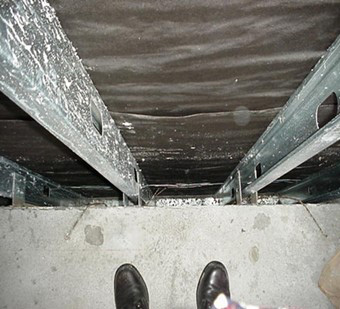
Suppose an EJ that includes disclaimers similar to “curtain wall design by others” nevertheless indicates an hourly rating (F-rating); it can typically be assumed unless explained otherwise, that this EJ would not achieve the stated rating if tested to ASTM E2307. The developer of the EJ is communicating they have knowledge about the behaviour of the joint sealant materials but that they do not have sufficient understanding of the fire behaviour of the curtain wall itself and how that could impact the joint sealants.
As a best practice, many manufacturers will provide a clear conclusion regarding the expected fire performance within a well-justified EJ, stating something similar to “design represents a firestop system expected to pass ASTM E2307 if tested.” However, do not expect to see the opposite conclusion stated as clearly, that the details shown would likely not pass the fire test or that the fire rating cannot be predicted. The latter case is indicated more subtly by one of the disclaimers discussed above or by the statement “smoke seal only.”
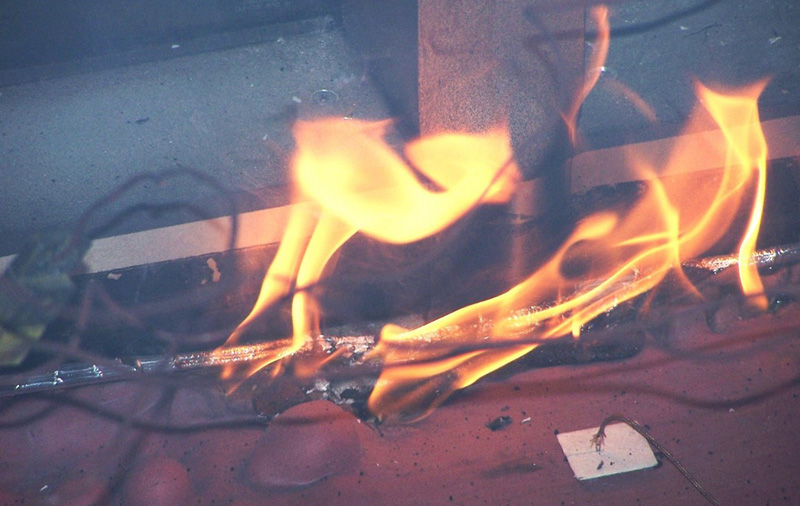
Conclusion
NBC 2020 now has requirements for firestopping the joint (gap) between the edge-of-slab and a curtain wall that harmonizes with the requirements in many other developed countries. It has done this by requiring perimeter joint firestopping that has been tested to ASTM E2307.
It is up to the specifier, designer, contractor, AHJ, and others in the construction chain to be alert of the possibility that a proposed firestop system listing or proposed EJ might not match the conditions of the curtain wall being constructed closely enough and that alternatives should be sought. Lack of a suitable match from one manufacturer could necessitate contacting other firestop product and system suppliers, who might have testing and listings that provide a closer match to the details of the curtain wall that is to be constructed. One should not assume that the company a contractor typically relies on for firestopping has the solutions for every curtain wall.
It could be the design details of a curtain wall under construction are so far removed from the 500-plus available Intertek and UL listings that no available firestop manufacturer has a system close enough to use as listed or per an EJ with reasonable extrapolation. Some curtain wall construction details cause an ASTM E2307 fire test to fail before achieving a minimal one-hour F-rating. If the proposed construction is thought to be able to pass a fire test, but there is not sufficient fire test data available to develop and justify an EJ, a commissioned fire test to ASTM E2307 could be needed to determine whether a proposed solution will provide the required F-rating. Building designers should be advised that the lead time for large-scale testing is typically many months, costing more than $40,000 per test. If that is the chosen path, one should seek out a firestop manufacturer with extensive fire test experience to guide this design process, or otherwise be ready to do multiple tests if a successful solution is not established on a first attempt. Even manufacturers with decades of perimeter joint firestop fire test experience will fail some tests when they try new conditions significantly different than what they have tested before. Modifying a curtain wall assembly to pass ASTM E2307 for the needed F-rating can sometimes be a trial-and-error process.
Terminology
Joint firestopping designed and tested to prevent vertical fire spread at the gap between a fire-resistance-rated floor slab and
a curtain wall is commonly referred to using many different terms. This article will refer to it as “perimeter joint firestopping.” This is consistent with the term used in the Canadian fire test method CAN/ULC-S115. Such firestopping is also commonly referred to as:
- Perimeter fire barrier (refer to ASTM E2307)
- Perimeter fire containment (refer to IBC)
- Edge-of-slab firestopping
- Curtain wall firestopping
- Perimeter gap firestopping
All these terms usually refer to systems tested to ASTM E2307.
Author
John Valiulis is director of codes and standards with Hilti North America. He has 39 years of experience working in multiple countries as a fire protection engineer in research, construction applications, and national codes and standards development. He holds degrees in chemical engineering and fire protection engineering. Valiulis has instructed fire protection engineering seminars in North America, South America, Europe, Asia, the Middle East, and the Caribbean and has written for many U.S. and Canadian publications. He has served on six NFPA technical committees and numerous ASTM committees.
He has contributed to developing the National Building Code of Canada (NBC) and the International Building Code (IBC). Valiulis
can be reached at john.valiulis@hilti.com.