Next-gen construction: Advancing 3D concrete printing in northern architecture
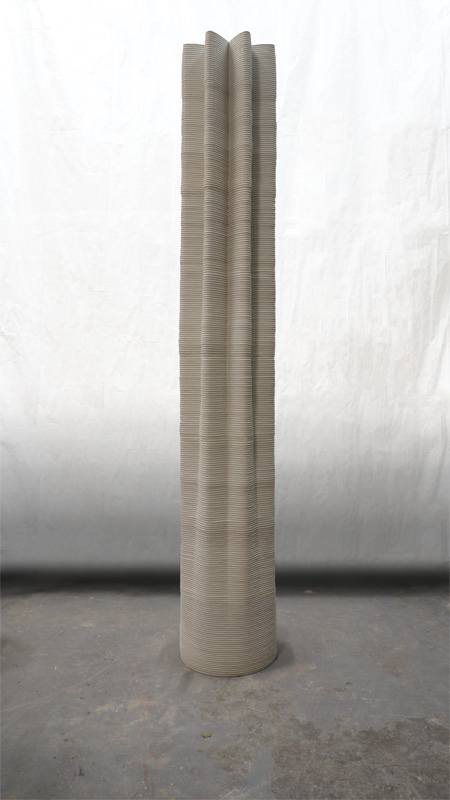
In recent years, 3D concrete printing (3DCP) has been reshaping the architecture and construction industries, moving beyond its experimental origins to become a viable method for producing complex, high-performance structures. No longer constrained by the limitations of traditional formwork, designers and architects can now explore new possibilities in geometry, expression, and construction tectonics, expanding what concrete can be and do.
Advanced digital technologies create intricate, non-standard volumes that were once impractical or impossible to fabricate with conventional materials and methods. Once the exclusive domain of skilled stonemasons, detailed and expressive architectural elements can now be produced through advanced digital fabrication, marking a new paradigm within the industry. A prime example is the first 3D-printed unreinforced concrete pedestrian bridge in Venice, built by the Block Research Group, in collaboration with Zaha Hadid Architects (ZHA). This project illustrates the ability of 3DCP to manufacture structurally efficient designs that save a substantial amount of material compared to formwork-based solutions, as no use of steel reinforcement or mortar was needed.
3DCP offers promising opportunities that align with regional environmental goals and the functional demands of northern climates. Through computational design and geometric optimization, 3DCP enables highly customizable building forms that improve thermal performance, reduce operational energy use, and enhance durability against harsh weather conditions. These capabilities are particularly relevant in northern regions, where resilience and energy efficiency are essential performance criteria. As Alami et al. (2023) note, “the utilization of 3D printing has the potential to enhance the thermal insulation of buildings and decrease energy usage, resulting in structures that provide improved thermal comfort. This can be achieved by printing geometries that are specifically designed for superior thermal insulation, such as cellular or lattice structures, or by altering the printing mix to include aerogels or air bubbles.” In addition, the technology promotes resource efficiency, generates less material waste compared to single-use custom formworks, and supports alternative low-carbon concrete mixes. This approach aligns with Canada’s commitment to carbon neutrality and sustainability. In the Northern region’s high-grade building codes for high-performance durability, safety, and efficiency, the application of 3D printing technology in construction necessitates a modification of these regulations. It does so, however, with fresh avenues of prefabrication and modularity, reducing construction time without compromising high-performance standards. By integrating these advancements, 3DCP has the potential to redefine architectural practice in northern climates, offering a year-long solution for production.
With the construction sector currently under pressure to improve efficiency and a shortage of typically skilled labour, automated concrete 3D printing is being explored as an alternative building strategy capable of reducing construction material waste. As cement production contributes to around eight per cent of the global CO2 emissions, the need for more resource-efficient approaches has never been greater (Placzek & Schwerdtner, 2023). By challenging conventional construction methods and harnessing the distinct possibilities of additive manufacturing, architects and engineers can redefine the limits of modern building practices.
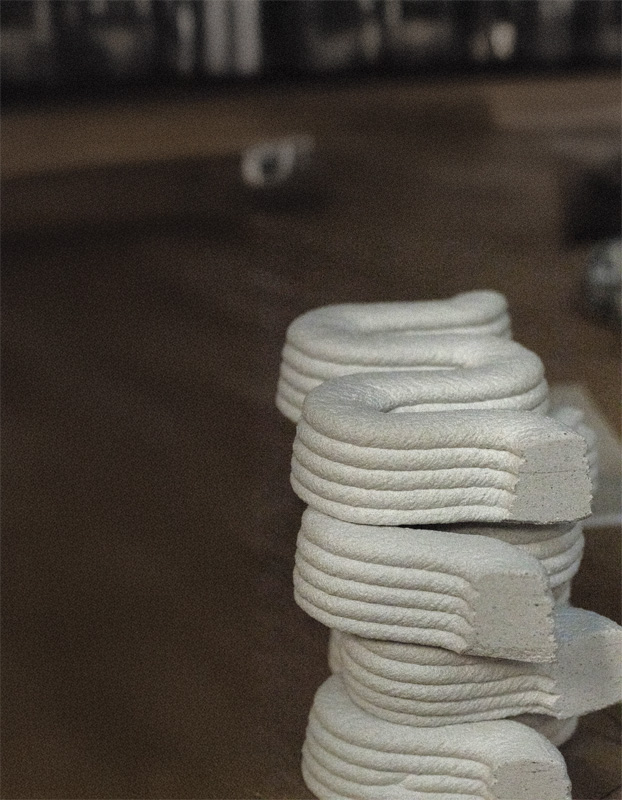
3DCP technology and advantages
Understanding 3DCP
At its core, 3DCP involves extruding specially formulated concrete layer upon layer. This process is known as additive manufacturing or, more commonly, 3D printing. Such concrete mixtures are usually made using hydraulic binders, aggregates, and additives. Generally, 3D models are processed through a slicing algorithm to produce a specific toolpath adapted to the chosen printing system. The three main technologies that account for most 3DCP are: robotic arms, gantry systems, and mobile crane systems.
- Robotic arm systems: A robotic arm system comprises multiaxis robotic arms with a specialized printhead attached to extrude concrete. They can produce complex, non-planar geometry and fine detail due to their wide range of motion, making them appropriate for custom models. The build volume is limited by the working length of the robotic arm. Therefore, larger structures may need to be prefabricated into smaller sections to assemble on-site. To increase their operational footprint, robotic arms can be installed on rail systems, enabling them to move along extended paths and fabricate larger components.
- Gantry systems: Gantry-based 3D printers operate on a Cartesian co-ordinate system, moving the printhead along fixed axes over a large build area. This configuration is well-suited for large-scale, repetitive building designs that produce long structural elements. The modular nature of gantry systems enables scalability, with some designs capable of constructing entire buildings in a single print sequence. Bod 2 by COBOD marks this category. However, the gantry systems may require independent foundations to generate additional constraints and costs (COBOD, n.d.).
- Mobile crane-based systems: Systems such as the MaxiPrinter by Constructions-3D blur the line between robotic automation and construction equipment. Functionally closer to a crane than a traditional robotic arm, the mobile crane system features a long, articulated printhead mounted on a mobile tracked chassis. It can be repositioned across a prepared site, allowing for extended build areas without the infrastructure required by gantry systems. While it lacks the fine motion control of industrial robotic arms, its mobility and scale make it well-suited for large structural prints in open environments (Constructions-3D, n.d.).
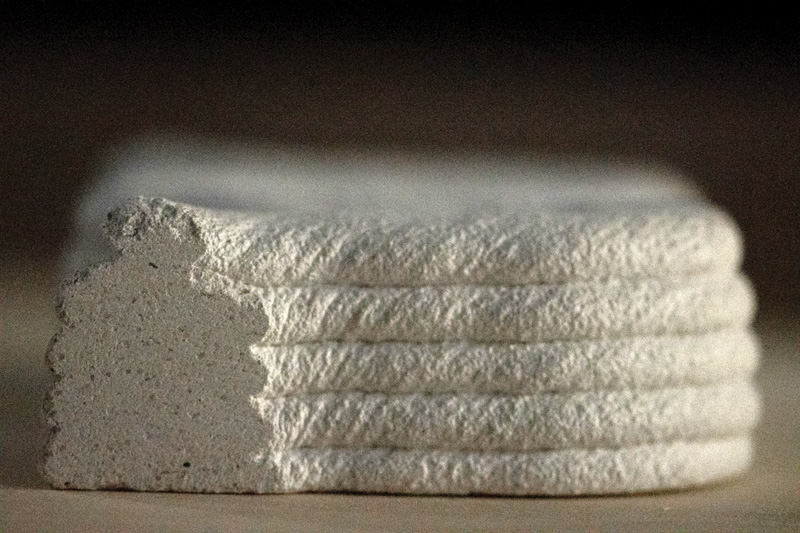
Three critical factors contribute to the effectiveness of 3DCP: printing speed, geometry, and rheology. Rheology refers to the study of how materials flow and deform, particularly focusing on their plasticity and suitability for pumping. In concrete printing, rheology primarily involves yield stress, the minimum stress required for the concrete to transition from solid-like to fluid-like behavior, enabling extrusion (Khan et al., 2023).
To achieve rapid solidification, essential for structural integrity, 3DCP mixtures typically contain two to three times the amount of cement found in ordinary premixed concrete. This higher cement content significantly accelerates setting times, often resulting in solidification within minutes. Due to this rapid curing, concrete must be deposited within that setting time to ensure cohesive bonding between each layer. This time span varies from one concrete mix design to another. Precise timing and rheological control are thus critical to achieving optimal adhesion and minimizing defects (Le et al., 2012).
While the cement proportion is elevated, the overall volume of material required per component is often significantly reduced. 3DCP enables geometrically optimized designs, such as hollow or ribbed structures, that use far less concrete than conventional cast elements. As a result, the total cement consumption per project can be lower, helping offset the mix’s higher concentration. This material efficiency translates into a reduced carbon footprint when assessed at the building or system level. Moreover, ongoing advances in printable low-carbon mixes and binder technologies continue to improve the sustainability profile of 3D printed concrete.
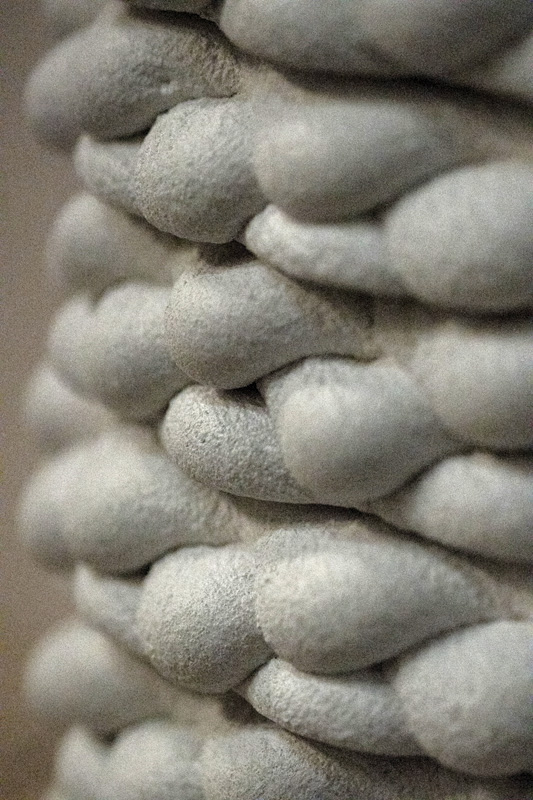
Digital tectonics and design expression
The potential of 3DCP inspires a rethinking of architectural design principles and tectonic expression. Parametric and organic shapes and structurally optimized designs become achievable, enabling novel esthetic outcomes (3Dnatives, n.d.).
The inherent layering process of 3DCP introduces a new tectonic language in architecture. Designers can use the exposed stratification and layering patterns as expressive tools, giving buildings distinct identities. This method enables an honest expression of materiality and construction process, aligning with contemporary architectural trends that focus on authenticity in materials and processes (3Dnatives, n.d.). 3DCP inherently facilitates the expression of bespoke textures and patterns within the fabrication process. Controlled layer deposition creates stratified effects, while varying the extrusion path produces raised patterns, enhancing the tactile and visual qualities of concrete surfaces. This capability contrasts with traditional methods, which inevitably require additional preparation and finishing steps to achieve similar results (3D Concrete Printing Solutions | Vertico, n.d.).
The precision and versatility of 3DCP make it especially ideal for custom-designed projects such as facades, urban furniture, and sculptural installations. A compelling example is Tor Alva, the world’s tallest 3D concrete printed tower, designed by ETH Zurich and built in the Swiss Alps. The project demonstrates how 3DCP enables expressive architectural forms, such as twisted geometries and perforated surfaces, that would be prohibitively complex using traditional methods. Beyond its architectural significance, Tor Alva is a cultural and touristic landmark, showing how 3DCP can help small communities attract visitors, support local identity, and promote sustainable economic development (ETH Zurich, 2023).
Optimization and productivity gains
Integrating 3DCP into the construction sector has introduced significant productivity, cost efficiency, and construction logistics advances. By enabling direct fabrication from digital models, 3DCP eliminates the need for traditional formwork, a process representing up to 50 per cent of total costs in conventional concrete construction (Jipa & Dillenburger, 2021; Placzek & Schwerdtner, 2023). This transition lowers the material demands and the substantial workforce typically required for casing assembly and disassembly, which is especially pertinent considering the skilled labour shortage in the construction industry (Placzek & Schwerdtner, 2023).
The automation of the printing process facilitates continuous, precise, and repeatable fabrication. This reduces human error and increases overall productivity while maintaining the possibility of custom pieces and small production runs. This is especially beneficial on construction sites where timelines and workforce availability are constrained. Additionally, the elimination of manual formwork allows for faster lead times between design and production and mitigates delays associated with conventional construction sequencing (Wangler et al., 2016).
Moreover, eliminating casing contributes significantly to waste reduction, particularly in the context of custom architecture. While standard and linear formwork systems can often be reused across multiple projects, the growing demand for distinctive architectural forms frequently requires custom moulds that are typically used only once. These bespoke formworks are rarely repurposed and often end up as waste, especially when made from plywood or expanded polystyrene. In such cases, 3DCP provides a highly efficient alternative by enabling the direct fabrication of complex geometries. This not only reduces construction waste but also avoids the environmental impact of over-dimensioned components, which have cascading environmental impacts throughout a building’s life-cycle (Jipa & Dillenburger, 2021). The precision of robotic printing further improves build quality and reduces the need for rework on-site, thereby minimizing resource consumption.
Beyond reducing labour and construction time, 3DCP, therefore, significantly improves material efficiency by enabling the fabrication of geometrically optimized components. For example, topology-optimized slabs, columns, and beams can be produced using minimal material while maintaining or enhancing structural performance (Jipa & Dillenburger, 2021).
Today, applications range from residential housing and smaller architectural elements to large-scale commercial projects. These include prefabricated structural walls, hollow columns with internal post-tensioning, and complex hybrid components that serve both structural and architectural roles. This versatility positions 3DCP as a key innovation in the shift toward more sustainable, efficient, and customizable construction methods.
A hybrid approach is emerging as the most practical route for large-scale adoption, combining the geometric freedom of 3D printing with traditional construction techniques. By using additive manufacturing for optimized forms and integrating conventional reinforcement where necessary, the industry can achieve both material savings and structural reliability (Placzek & Schwerdtner, 2023). 3DCP enables the creation of hollow forms, strategic material placement, and structural reinforcement through infill patterns. It also supports embedded features such as pockets for lost formwork, onsite casting zones, and seamless integration with reinforcing bars.
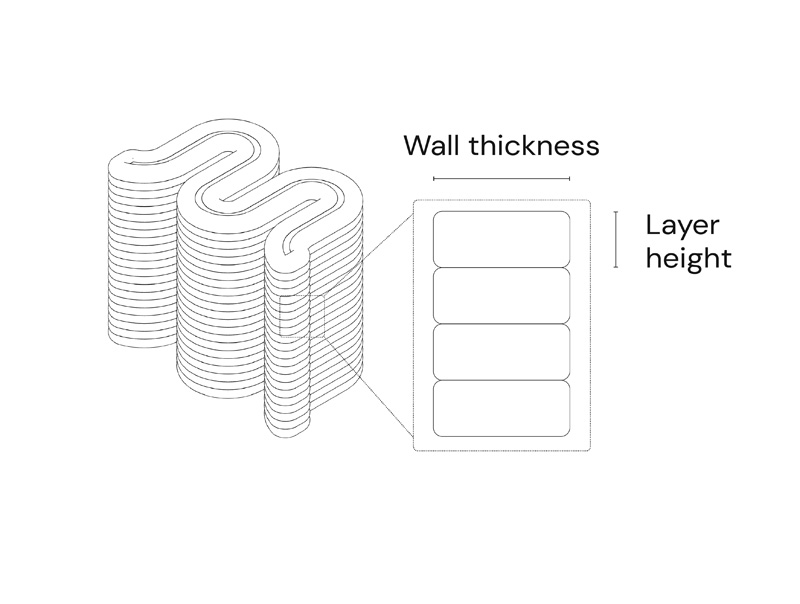
Material challenges in cold climates
Current state of materials in the Canadian market
The Canadian market for 3DCP is currently expanding, with several local companies developing proprietary mixes tailored to their specific printing systems. However, global leaders such as Sika and Mapei also provide ready-to-use premixes adapted to the demands of additive manufacturing. In a recent move to support regional adoption, Sika has established local production of its 3D printable concrete in Montreal. This shift not only lowers importation costs but also reduces environmental impacts related to transportation and improves supply reliability for Canadian operators (Sika Canada, 2024).
The Canadian climate poses additional material challenges. Printable concrete must demonstrate freeze-thaw resistance and maintain mechanical integrity under severe winter conditions. While manufacturers often claim high structural performance, including compressive strengths exceeding 30 MPa (4.35 ksi),
many commercially available mixes still lack formal testing according to CSA standards, particularly regarding fire resistance and durability under freeze-thaw cycles (Silveira et al., 2024; Wagner et al., 2024).
The complexity of 3DCP introduces another key issue: high sensitivity to variations in mix composition. Even minor deviations in water content, admixtures, or curing conditions can lead to significant impacts on printability and structural performance (Silveira et al., 2024). These inconsistencies pose operational risks and highlight the critical importance of locally produced, quality-controlled mixes.19 In their 2024 study on material performance in 3D printed concrete, Wagner et al. reported that a proprietary mix used for full-scale printed elements exhibited about 40 per cent lower compressive strength than its mold-cast counterpart. This finding highlights the ongoing challenges in achieving reliable structural performance in layered additive construction while new 3D concrete mixtures are launched on the market (Wagner et al., 2024).
Despite these hurdles, there is clear momentum toward the standardization of materials. Active efforts are underway to develop adapted testing protocols and validate materials against Canadian building codes. These steps are essential for enabling the full integration of 3DCP in structural applications within the country’s regulatory framework.
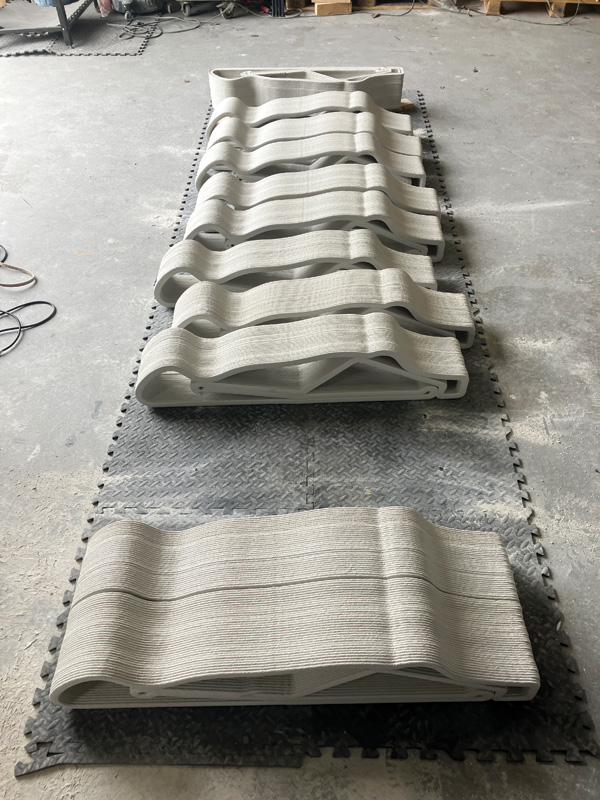
Toward more sustainable and high-performance materials
When cured and cut, layers in 3DCP typically show no visible seams, except for traces left by cutting tools. The use of fine aggregates
0–2 mm (0–0.08 in.) in 3DCP significantly enhances mechanical properties, allowing compressive strength to reach approximately 50 MPa (7.25 ksi), which is almost double the strength of conventional foundation concrete (Tran et al., 2024).
The construction industry is actively seeking innovative solutions to reduce its carbon footprint by developing more environmentally responsible materials. Among these efforts, the author’s company has developed a bio-concrete with the capacity to capture 348 kg (767 lb) of CO2 per square metre, a significant improvement compared to traditional concrete mixes. This innovation holds strong promises for decarbonizing the construction sector, particularly when coupled with robotic 3D printing technologies that further optimize material use. It is best suited for non-structural applications and used for its isolation properties (Medusia, 2024).
Internationally, the use of natural materials such as clay and earth in 3D printing has gained traction as a low-impact alternative. In the United States, the practice has been notably advanced by Rael San Fratello, whose research explores large-scale 3D printing with regionally sourced soils. Through projects such as Mud Frontiers, they demonstrate how locally sourced materials and robotic fabrication can merge to produce affordable, biodegradable structures that are both environmentally responsive and culturally rooted, offering a sustainable pathway for construction in arid and rural regions (Rael San Fratello, 2024).
The Gramazio Kohler Research group is also exploring similar directions with its “Impact Printing” method—a gravity-driven additive construction process that uses clay instead of concrete. By eliminating the need for formwork, binders, and energy-intensive hardening processes, this technique drastically lowers the environmental impact of fabrication. Impact Printing allows for high levels of geometrical freedom, is reversible (since clay is reusable), and offers true circularity in construction workflows (Etherington, 2024).
In addition to structural applications, ceramic 3D printing is becoming a medium for esthetic and cultural innovation. Studio RAP (Netherlands) exemplifies this approach with its “New Delft Blue” project, which combines algorithmic design and robotic 3D printing to create custom ceramic facade tiles inspired by traditional Dutch craftsmanship. The process minimizes waste and allows for local, small-batch fabrication using naturally derived materials (Studio RAP, 2023).
As material science evolves, the shift toward high-performance, low-carbon, and locally sourced printable materials appears essential for the future of sustainable construction.
Technical aspects and regulatory framework
Reinforcement integration and structural performance
One of the critical technical challenges in 3DCP is the integration of reinforcement within printed structures. Unlike traditional concrete construction, where reinforcement bars are embedded in cast elements, 3DCP must contend with the layering process, which often restricts the direct integration of rebar. Researchers such as Silveira et al. (2024) have explored methods such as incorporating vertical reinforcement cages post-printing or developing interlocking geometries to improve cohesion between layers. Their experiments demonstrated that properly reinforced 3D printed walls under axial compression can achieve structural behaviour comparable to traditional systems, provided the interface between layers and reinforcement is adequately managed.
Wagner et al. (2024) further emphasize the importance of rethinking the structural design paradigm. Rather than attempting to replicate monolithic concrete behaviour with inferior layer adhesion, 3DCP allows for more efficient shell and arch-like structural logic using high-performance concrete mixes. This shifts the focus from over-dimensioned solid concrete elements to thin-walled structures where strength derives from geometry and material quality, not mass. However, such optimization requires engineers to familiarize themselves with digital fabrication workflows, parametric modelling, and the non-uniform behaviour of layered materials (Inozemtcev, 2024).
To illustrate, a typical 3D-printed wall composition might involve a double-skin concrete extrusion with an internal cavity for insulation or reinforcement. Post-tensioning, short-fibre additions, or metal rods inserted between layers are among the methods being tested for load-bearing performance (Inozemtcev, 2024). These developments demand new competency from structural engineers, who must assess printed components not as conventional masses of concrete but as engineered shells with differentiated mechanical behaviour.
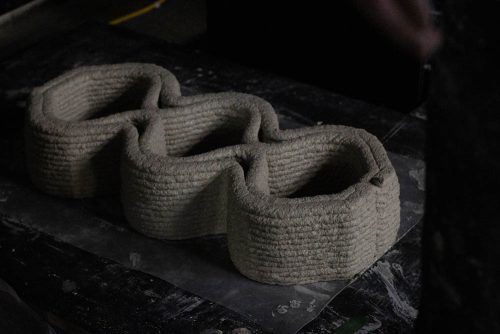
Building codes and regulatory challenges
The adoption of 3D-printed concrete in the construction industry remains constrained by the absence of standardized testing protocols and formal recognition within building codes. In Canada, for example, printed structures do not yet meet the full requirements of CSA A23.3 for reinforced concrete due to unresolved issues related to fire resistance, freeze-thaw durability, and long-term performance (Silveira et al., 2024). As a result, 3D-printed homes in Canada typically require case-by-case approvals, often involving special permits or engineering justifications. These regulatory uncertainties present a major barrier to scaling the technology and integrating it into mainstream construction workflows.
To support wider adoption, building codes must evolve to reflect the specific mechanical behavior of printed elements, particularly their anisotropic properties, the bond strength between layers, and alternative reinforcement strategies. Without dedicated provisions for these features, 3D-printed components remain difficult to certify under existing structural design standards.
ISO/ASTM 52939:2023, Additive Manufacturing for Construction—Qualification Principles—Structural and Infrastructure Elements, offers an initial framework to address some of these challenges. The standard sets out quality assurance principles for non-metallic additive construction processes and applies to both load-bearing and non-load-bearing elements in residential and commercial projects. It emphasizes the control of process conditions and quality-relevant parameters on-site to promote safe and consistent practices in large-scale 3D printing.
However, ISO/ASTM 52939 has not yet been formally adopted in Canada. According to the Standards Council of Canada, the standard currently holds no regulatory status, limiting its enforceability within national frameworks. The absence of a national standard also reinforces the need for printed components to be reviewed by locally certified engineers and to comply with regional codes. This further highlights the importance of integrating new standards with existing regulatory systems.
Continued efforts are required to adopt such standards to national contexts and align them with evolving building codes, enabling the broader industrial deployment of 3D printing technologies in construction.
Conclusion
The next steps in advancing concrete 3D printing will focus on improving reinforcement strategies, refining printable material formulations, and expanding on-site capabilities. These developments will be instrumental in transitioning additive manufacturing from a niche technology to a widely adopted construction method (Placzek & Schwerdtner, 2023).
The future of 3DCP in Canada hinges not only on continued technical innovation but also on the evolution of regulatory frameworks that can accommodate and certify this emerging construction method. For 3DCP to scale beyond prototypes and one-off projects, its acceptance by authorities such as the National Research Council (NRC) and the Canadian Board for Harmonized Construction Codes (CBHCC) is essential. These organizations play a pivotal role in integrating new materials and methods into the National Building Code (NBC), a prerequisite for mainstream adoption. The NRC’s initiatives, such as the Additive Construction Consultation Workshop held in January 2025 in Toronto, are already advancing development in the right direction by effectively bringing together key Canadian 3DCP stakeholders.
Research and development are central to this transition. Standardized testing for fire resistance, freeze-thaw durability, and mechanical performance must be developed and validated under Canadian climatic conditions. The lack of such data currently impedes regulatory approval, even as early results demonstrate that printed structures can meet or exceed traditional benchmarks when properly designed and reinforced (Silveira et al., 2024; Wagner et al., 2024).
In Quebec, the Innovative Group for Sustainable Building Printing (RI³D-FRQNT) is actively bridging the regulatory and technical gaps that currently limit the deployment of 3DCP. This interdisciplinary initiative, uniting academic institutions and industrial partners, aims to develop localized performance benchmarks, testing protocols, and certification frameworks tailored to the Canadian context. RI³D’s work supports the broader evolution of building codes, ensuring that emerging digital construction methods are recognized and responsibly integrated into national standards.
To accelerate adoption, a focus on prefabrication aims to integrate this technology progressively into existing workflows. 3DCP components can already be integrated into diverse building types, from multifamily residential projects to hotels, museums, and retail spaces, as soon as today (Medusia, 2024). However, scaling its impact will require several key steps: the development of national certification pathways for 3D-printed elements, the promotion of pilot projects in collaboration with municipalities, and stronger partnerships between academia, industry, and regulators. With these in place, 3DCP could become a cornerstone of Canada’s low-carbon, high-efficiency buildings, transforming how we build and define architectural and structural standards in the 21st century.
Resources
- Alami, A. H., Olabi, A. G., Ayoub, M., Aljaghoub, H., Alasad, S., & Abdelkareem, M. A. (2023). “3D Concrete Printing: Recent Progress, Applications, Challenges, and Role in Achieving Sustainable Development Goals.” Buildings, 13(4), 924. See doi.org/10.3390/buildings13040924
- Anton, A., Jipa, A., Bernhard, M., & Dillenburger, B. (2024). “A comprehensive review of sustainable materials and toolpath design in 3D concrete printing.” Nature Reviews Materials. See nature.com/articles/s44296-024-00017-9
- COBOD International. (2023). “Robotic arm vs. gantry 3D concrete printer.” COBOD International. Retrieved March 24, 2025, from cobod.com/robotic-arm-vs-gantry-3d-concrete-printer
- COBOD. (n.d.). “Robotic arm vs gantry 3D concrete printer” at cobod.com/robotic-arm-vs-gantry-3d-concrete-printer/
- Constructions-3D. (n.d.). MaxiPrinter. See constructions-3d.com/en/maxiprinter
- Etherington, S. (2024). “Is ETH Zurich’s unique Impact Printing construction method a sustainable alternative to 3D printing? 3D Printing Industry.” 3dprintingindustry.com/news/is-eth-zurichs-unique-impact-printing-construction-method-a-sustainable-alternative-to-3d-printing-234021/
- ETH Zurich. (2023). Tor Alva – The tallest 3D-printed tower made of clay. https://ethz.ch/en/news-and-events/eth-news/news/2023/11/tor-alva-the-worlds-tallest-3d-printed-clay-tower.html
- International Organization for Standardization (ISO). (2023). ISO/ASTM 52939:2023 – Additive manufacturing for construction — Qualification principles — Structural and infrastructure elements. https://www.iso.org/standard/81177.html
- Inozemtcev, A. S. (2024). Modern theory and practice of concrete technology for 3D printing in construction. Vestnik MGSU, 19(2), 216–245. https://doi.org/10.22227/1997-0935.2024.2.216-245
- Jipa, A., & Dillenburger, B. (2021). 3D printed formwork for concrete: State-of-the-art, opportunities, challenges, and applications. 3D Printing and Additive Manufacturing. https://doi.org/10.1089/3dp.2021.0024
- Khan, K., Ahmad, W., Farooq, F., & Lee, D. J. (2023). Rheological properties of cementitious composites for 3D concrete printing: A comprehensive review. Materials, 16(21), Article 6864. https://doi.org/10.3390/ma16216864
- Le, T. T., Austin, S. A., Lim, S., Buswell, R. A., Gibb, A. G. F., & Thorpe, T. (2012). Mix design and fresh properties for high-performance printing concrete. Materials and Structures, 45(8), 1221-1232. https://doi.org/10.1617/s11527-012-9828-z
- Medusia. (2024). Bio-concrete and sustainable 3D printing. Retrieved from https://medusia.ca
- Placzek, G., & Schwerdtner, P. (2023). Concrete additive manufacturing in construction: Integration based on component-related fabrication strategies. Buildings, 13(1769). https://doi.org/10.3390/buildings13071769
- Rael, R., & San Fratello, V. (2020). Mud Frontiers: Experiments in hand-built and robotically printed architecture. Emerging Objects. Retrieved from https://www.rael-sanfratello.com/made/mud-frontiers
- Sika Canada. (2024). 3D Concrete Printing Solutions. Retrieved from https://can.sika.com/en/construction/concrete-admixtures/3d-concrete-printing.html
- Silveira, M. V. G., Wagner, J. S., Khanverdi, M., & Das, S. (2024). Structural performance of large-scale 3D-printed walls subjected to axial compression load. Canadian Journal of Civil Engineering, 51(2), 919–933. https://doi.org/10.1139/cjce-2023-0395
- Silveira, J., Doyon, A., Boulanger, P., & Massicotte, B. (2024). Assessment of structural design requirements for 3D-printed concrete in Canada. Journal of Advanced Construction Technology, 12(1), 45–62.
- Standards Council of Canada (SCC). (n.d.). Standards database entry for ISO/ASTM 52939. Retrieved March 26, 2025, from https://scc-ccn.ca/standardsdb/standards/8185383
- Studio RAP. (2023). New Delft Blue: 3D printed ceramic facade. Retrieved from https://www.designboom.com/architecture/new-delft-blue-studio-rap-3d-printed-tiles-netherlands-08-24-2023/
- Tran, N., Tran, M. V., Tran, P., Nguyen, A. K., & Nguyen, C. Q. (2024). Eco-friendly 3D-printed concrete using steel slag aggregate: Buildability, printability and mechanical properties. International Journal of Concrete Structures and Materials, 18, Article 66. https://doi.org/10.1186/s40069-024-00705-9
- Vertico. (n.d.). 3D concrete printing solutions: How it’s reshaping design. Vertico. Retrieved March 24, 2025, from https://www.vertico.com/wiki/3d-printed-facades-architecture
- Wagner, J. S., Silveira, M. V. G., Vanderlei, R. D., & Das, S. (2024). Comparative analysis of mold-cast and 3D-printed cement-based components: Implications for standardization in additive construction. Canadian Journal of Civil Engineering. https://doi.org/10.1139/cjce-2024-0169
- Wangler, T., Lloret, E., Reiter, L., Hack, N., Gramazio, F., Kohler, M., & Flatt, R. J. (2016). Digital Concrete: Opportunities and challenges. RILEM Technical Letters, 1, 67–75. https://doi.org/10.21809/rilemtechlett.2016.16
- WASP. (2023). TECLA: 3D printed eco-habitat made with local earth. Retrieved from https://www.3dwasp.com/en/project-tecla/
- 3Dnatives. (2020). 3D concrete printing: A new dimension in construction. 3Dnatives. Retrieved March 24, 2025, from https://www.3dnatives.com/en/3d-printing-in-architecture-121120204/
Author
Gabrielle Nadeau, M.Arch, is a project manager at Medusia. She oversees product development and marketing strategy, focusing on advancing 3D printing technology and its applications. Her work in AI explorations and 3D modelling enhances Medusia’s creative approach, bringing fresh, tailored solutions that resonate with both functionality and design innovation.