Specifying steel curtain walls with enduring beauty
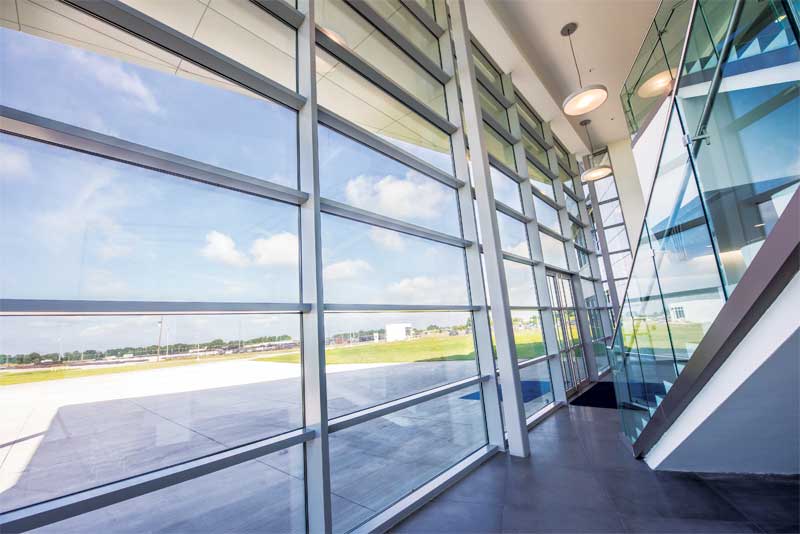
Moisture intrusion
Advanced steel curtain wall assemblies resolve an important performance challenge—preventing water in the glazing cavity from coming into direct contact with the steel frame. By incorporating a continuous gasket across the full width of the steel frame, they can provide sufficient protection against dynamic and static water penetration, and reduce the potential for corrosion.
For example, steel frames with continuous gasketing keep water off the tops of insulated glass (IG) units and direct it to the verticals. Installers then must ensure performance by sealing the lapped gasket joints at horizontal-to-vertical connections to prevent water intrusion to the steel back members and interior occupied spaces.
As an added benefit, these systems do not require zone damming at each glazed lite to help manage water flow within the system, as is typical with aluminum pressure plate systems. The full gasketing fabrication method without zone damming still provides a water penetration resistance of 718 Pa (15 psf), meeting ASTM E331, Standard Test Method for Water Penetration of Exterior Windows, Skylights, Doors, and Curtain Walls by Uniform Air Pressure Difference.
To ensure greater protection from corrosion once the building is completed, some steel systems employ more-conventional aluminum or stainless steel cover caps and pressure plates to retain the glass to the framing. They rely on self-sealing fasteners that penetrate the glazing, while simultaneously blocking access for water penetration. When using structural silicone glazing, sealants specific to the application are available. They hold the glass to the framing in lieu of pressure plates and covers, as is typical with captured curtain wall systems.
Installers can also place watertight weather seals around the perimeter of the framing. The seals are made to gaskets at the back of the glazing pocket. Typically, they are made to special extrusions or to perimeter details in plane with the glass instead of to the framing. By placing perimeter seals in front of the steel, the installer eliminates any chance of water contacting the material behind the seal.
Even though stainless steel has improved resistance against corrosion, many features are the same when using stainless steel for the frame gasketing. The edge seal details are similar for either material, and both can offer the same air- and water-penetration resistance.
To further simplify and standardize fabrication and installation for both materials, while still meeting the higher performance criteria of modern curtain wall construction, steel curtain wall system suppliers have developed all component parts to the point where a complete system is often available, including:
- connection detailing and hardware;
- gasketing;
- exterior pressure plates and cover caps; and
- complementary door and entry systems, as well as detailing.
Due to the full gasketing across the face of the systems at the back of the glazing pocket, some steel curtain wall systems can provide even greater protection against the elements. For example, water resistance can be as much as 25 per cent greater in an off-the-shelf steel curtain wall assembly than with a conventional extruded aluminum curtain wall. Additionally, air penetration is almost non-existent in steel curtain walls due to the full gasketing, testing to as low as 0.1 cf/sf of wall (per ASTM E283, Standard Test Method for Determining Rate of Air Leakage Through Exterior Windows, Curtain Walls, and Doors Under Specified Pressure Differences Across the Specimen, at 298.7-Pa [6.24-psf] pressure differential).
BRIDGING FIRE AND LIFE SAFETY WITH DESIGN GOALS |
Modern steel frames are advantageous not just for non-rated curtain wall systems, but also for fire-rated systems. In large part, this is due to advances in manufacturing techniques.
Steel fire-rated frames can be formed from tubes, instead of sheets, and shaped from coil stock in a rolling process. (This is similar to the way non-rated steel frames are fabricated, as discussed in the main article.) These fire-rated frames are more slender than the wrap-around form of traditional fire-rated ‘hollow-metal’ steel frames. They have narrow profiles, well-defined corners, and crisp edges. They can also be custom-painted or powder-coated, and can incorporate custom cover caps to match a wide array of design schemes. When these versatile steel fire-rated frames are engineered and manufactured as part of a complete fire-rated curtain wall system (where the fire-resistive glass, framing, and component parts have been designed to work together and meet the minimum fire rating for the entire system, in accordance with the National Building Code of Canada [NBC]), they can satisfy stringent fire and life safety criteria. For example, Canadian test standards that such fire-rated curtain wall systems meet include:
With exceptional fire resistance and enhanced versatility, these high-performing fire-rated curtain wall systems can help bring fire safety in line with the design intent. For example, one popular option is to specify fire-rated curtain walls with narrow steel frame profiles and custom cover caps. They allow design teams to more closely match the look of non-rated curtain wall systems, as was the case in the Fulton Center Transit Hub in New York City (shown on page 24). Grimshaw Architects, in conjunction with Arup, installed a non-rated and rated-steel curtain wall system with custom captured horizontal steel mullions to maintain a uniform look within the grand atrium’s two-level circular enclosed space. Design teams can also use the smooth, exterior surface of silicone-glazed fire-rated curtain walls to visually tie in with neighboring structural silicone glazed curtain wall systems. The system achieves a sleek, exterior appearance through a toggle retention system that becomes hidden once installed, thus eliminating the exterior pressure plate and cover cap of a conventionally captured system. Where it is desirable to install fire-rated glass walls in interior spaces with virtually uninterrupted views, design teams can select from one of the most recent options on the market—a butt-glazed fire-rated system. The fire-rated glass wall panels are installed relatively close together, with no back-up metal along the vertical edge of the glass. The top and bottom edges are installed in a fire-rated perimeter frame. The narrow, vertical glass joints are sealed, and create a continuous glass wall esthetic without vertical framing interrupting the view—a popular look that is often found in non-rated glazing applications. |